Was bedeutet Digitalisierung in der Produktion?
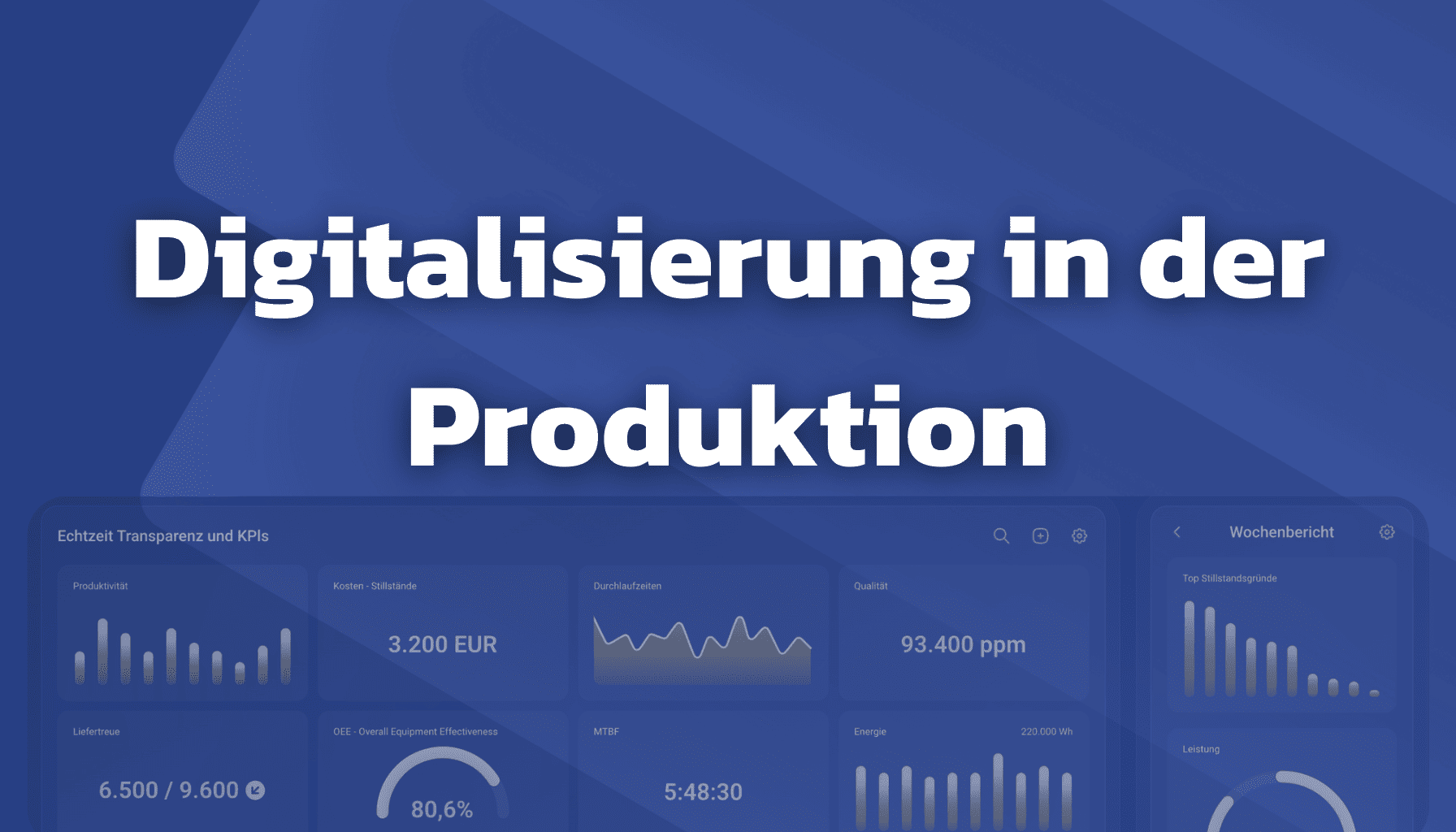
Inhaltsverzeichnis
- Was bedeutet Digitalisierung in der Produktion?
- Die Evolution der Produktionsdigitalisierung
- Die transformativen Vorteile der Produktionsdigitalisierung
- Digitalisierung und die Mensch-Maschine-Zusammenarbeit
- Kernelemente einer digitalisierten Produktion
- Der Weg zur digitalisierten Produktion
- Die Rolle von Cloud MES für die digitalisierte Produktion
- Herausforderungen der Produktionsdigitalisierung
- Die Zukunft der digitalisierten Produktion
- SYMESTIC: Revolutionäre Cloud-MES-Lösung
Definition
Die Digitalisierung in der Produktion bezeichnet den Einsatz vernetzter, digitaler und automatisierter Technologien in Fertigungsprozessen. Sie verbindet die physische Welt der Fertigung mit der digitalen Welt, um Transparenz zu schaffen, Prozesse zu optimieren und neue Geschäftsmodelle zu ermöglichen.
Die Digitalisierung umfasst die Erfassung, Strukturierung und Analyse von Daten sowie die Vernetzung von Maschinen, Prozessen und Produkten mittels moderner Technologien. Sie bildet das Fundament für Industrie 4.0 und unterscheidet sich von reiner Automatisierung durch ihre umfassende Vernetzung und intelligente Steuerung des gesamten Produktionssystems – vom Shopfloor bis zum Topfloor.
Die Digitalisierung der Fertigung hat sich in mehreren Stufen entwickelt:
- Konventionelle Automatisierung: Einzelne Maschinen werden automatisiert, arbeiten jedoch isoliert.
- Computergestützte Systeme: Einführung von CAD/CAM und computergestützter Prozesssteuerung.
- Vernetzte Systeme: Maschinen kommunizieren über lokale Netzwerke.
- Cloud-basierte Lösungen: Zentrale Datenspeicherung ermöglicht standortübergreifende Zusammenarbeit.
- Cloud-native Systeme: Lösungen, die von Grund auf für die Cloud entwickelt wurden, bieten maximale Flexibilität.
Moderne Unternehmen bewegen sich hin zu cloud-nativen Systemen, die als digitales Rückgrat die gesamte Fertigung steuern.
1. Drastische Effizienzsteigerung und Kostenreduktion
Digitalisierung steigert die Effizienz durch:
- Reduzierung von Stillstandzeiten: Echtzeit-Überwachung minimiert Ausfälle.
- Optimierte Ressourcennutzung: Effizienter Einsatz von Material und Energie.
- Automatisierte Prozesse: Digitale Workflows ersetzen manuelle Tätigkeiten.
- Kürzere Durchlaufzeiten: Optimierte Planung beschleunigt die Produktion.
Cloud-basierte MES-Systeme ermöglichen Einsparungen von 10-25% bei der Gesamtanlageneffektivität und 30-60% weniger Ausschuss.
2. Maximale Transparenz durch Echtzeit-Daten
Digitalisierte Produktion bietet:
- Echtzeit-Monitoring: Kontinuierliche Überwachung aller KPIs.
- Datenbasierte Entscheidungen: Präzise Daten statt Intuition.
- Frühwarnsysteme: Automatische Erkennung von Problemen.
- Rückverfolgbarkeit: Lückenlose Dokumentation.
3. Gesteigerte Flexibilität und Agilität
Flexibilität wird zum Wettbewerbsvorteil durch:
- Schnelle Produktwechsel: Kurze Umrüstzeiten.
- Individualisierte Produktion: Losgröße 1 wird wirtschaftlich.
- Skalierbarkeit: Anpassung an Nachfrage.
- Dynamische Planung: Sofortige Anpassung.
4. Verbesserte Qualität und Kundenzufriedenheit
Digitalisierung steigert die Qualität durch:
- Integrierte Qualitätskontrollen: Kontinuierliche Überwachung.
- Statistische Prozesskontrolle: Früherkennung von Abweichungen.
- Fehlerprävention: Digitale Assistenzsysteme.
- Konsistente Prozesse: Standardisierte Workflows.
Digitalisierung und die Mensch-Maschine-Zusammenarbeit
Digitalisierung schafft eine menschenzentrierte Produktion:
- Wegfall repetitiver Tätigkeiten: Monotone Aufgaben werden automatisiert.
- Neue Rollen: Mitarbeiter übernehmen Planung und Optimierung.
- Digitale Assistenzsysteme: Kontextbezogene Informationen unterstützen.
- Kollaborative Robotik: Mensch und Roboter arbeiten Hand in Hand.
Moderne MES-Systeme fördern die Produktivität durch intuitive Benutzeroberflächen und relevante Informationen zur richtigen Zeit.
Kernelemente einer digitalisierten Produktion
1. Vernetzte Maschinen und Anlagen (IIoT)
Das Industrial Internet of Things (IIoT) umfasst:
- Sensorik: Kontinuierliche Datenerfassung.
- Konnektivität: Maschinenkommunikation.
- Edge Computing: Dezentrale Datenverarbeitung.
- Retrofitting: Nachrüstung älterer Maschinen.
2. Manufacturing Execution Systeme (MES)
Ein MES verbindet Planung und Fertigung:
- Produktionsplanung: Optimale Ressourcennutzung.
- Materialmanagement: Steuerung des Materialflusses.
- Qualitätsmanagement: Integrierte Kontrollen.
- Personalmanagement: Qualifikationsplanung.
3. Datenanalyse und künstliche Intelligenz
Intelligente Nutzung von Daten durch:
- Beschreibende Analytik: Transparenz über Leistung.
- Diagnostische Analytik: Ursachenidentifikation.
- Prädiktive Analytik: Prognose von Problemen.
- Präskriptive Analytik: Optimale Handlungsoptionen.
Testen Sie die Digitalisierung mit SYMESTIC
Erleben Sie die Vorteile der digitalisierten Produktion mit unserem kostenlosen 30-Tage-Free-Trial von SYMESTIC. Starten Sie mit Echtzeit-Daten, optimierten Prozessen und transparenten KPIs – ohne Risiko.
Der Weg zur digitalisierten Produktion
Die Implementierung erfordert eine strategische Herangehensweise:
1. Analyse und Strategie
- Ist-Zustand analysieren
- Digitalisierungsstrategie entwickeln
- Use Cases mit hohem ROI identifizieren
- Passende Technologien auswählen
2. Pilotierung und schnelle Erfolge
- Pilotbereich auswählen
- Grundfunktionalitäten implementieren
- Schnelle Erfolge sichtbar machen
- Aus Erfahrungen lernen
Die Rolle von Cloud MES für die digitalisierte Produktion
Ein cloud-natives MES ist das Rückgrat der digitalisierten Produktion, das Maschinen, Prozesse und Menschen verbindet.
- Schnelle Implementierung: In Tagen einsatzbereit.
- Maximale Flexibilität: Modulare Anpassung.
- Skalierbarkeit: Mühelose Erweiterung.
- Kontinuierliche Innovation: Automatische Updates.
- Hohe Sicherheit: Professionelle Sicherheitsarchitektur.
Die Investition amortisiert sich typischerweise innerhalb von 3-12 Monaten.
Herausforderungen der Produktionsdigitalisierung
1. Datensicherheit und -souveränität
- Herausforderung: Sorge um sensible Daten.
- Lösung: Professionelle Sicherheitskonzepte und Verschlüsselung.
2. Integration bestehender Maschinen und Systeme
- Herausforderung: Ältere Maschinen ohne moderne Schnittstellen integrieren.
- Lösung: Edge-Gateways und IoT-Sensoren für Nachrüstung.
3. Mitarbeiterakzeptanz und -qualifikation
- Herausforderung: Widerstand gegen Veränderung und mangelnde digitale Kompetenzen.
- Lösung: Frühzeitige Einbindung, Schulungen und intuitive Benutzerschnittstellen.
4. Internetzuverlässigkeit und Offline-Fähigkeit
- Herausforderung: Sorge vor Ausfällen bei Internetstörungen.
- Lösung: Redundante Verbindungen, Edge-Computing und Offline-Fähigkeit.
Die Zukunft der digitalisierten Produktion
Die Digitalisierung entwickelt sich weiter mit zukunftsweisenden Trends:
1. Künstliche Intelligenz und Machine Learning
- Predictive Maintenance: Vorhersage von Ausfällen.
- Autonome Produktionsplanung: KI optimiert Sequenzen.
- Qualitätsprognose: Vorhersage von Qualitätsproblemen.
2. Digital Twins und Simulation
- Virtuelle Inbetriebnahme: Testen vor Umsetzung.
- Echtzeit-Optimierung: Anpassung durch Simulationen.
- Szenarienplanung: Was-wäre-wenn-Analysen.
3. Erweiterte und virtuelle Realität
- AR-gestützte Wartung: Visuelle Anleitungen.
- VR-Training: Realistische Schulung in virtuellen Umgebungen.
- Digitale Arbeitsanweisungen: Interaktive Anleitungen.
SYMESTIC: Revolutionäre Cloud-MES-Lösung
SYMESTIC setzt neue Maßstäbe mit seiner cloud-nativen MES-Lösung, die alle Funktionen für die digitale Transformation vereint:
- Modularer Aufbau: Flexible Module wie MDE, BDE und KI-Analysen.
- Schnelle Implementierung: Einsatzbereit in Tagen.
- Nahtlose Integration: Anbindung moderner und älterer Maschinen.
- Intuitive Bedienung: Benutzerfreundliche Dashboards.
SYMESTIC unterstützt Unternehmen weltweit bei der digitalen Transformation mit Erfolgen in Effizienz, Qualität und Kostensenkung.
Fazit: SYMESTIC bietet eine skalierbare, flexible Lösung, die Unternehmen zum digitalen Erfolg führt.
Fazit: Digitalisierung als Schlüssel zum Erfolg
Die Digitalisierung ist eine strategische Notwendigkeit für wettbewerbsfähige Unternehmen. Sie bietet transformative Vorteile:
- Effizienzsteigerung: Weniger Stillstände und kürzere Durchlaufzeiten.
- Transparenz: Echtzeit-Daten für fundierte Entscheidungen.
- Flexibilität: Anpassung an Marktanforderungen.
- Qualität: Weniger Fehler, höhere Kundenzufriedenheit.
„Wer heute nicht digitalisiert, wird morgen nicht mehr wettbewerbsfähig sein.“
Testen Sie Cloud MES kostenlos
Überzeugen Sie sich von den Vorteilen eines Cloud MES mit dem kostenlosen 30-Tage-Free-Trial von SYMESTIC. Binden Sie Anlagen an, gewinnen Sie Echtzeit-Daten und erkennen Sie Ihr Optimierungspotenzial – schnell und einfach.
- Einfache Anbindung: Verbinden Sie 1-2 Anlagen.
- Echtzeit-Daten: Erfassen Sie Daten für 30 Tage.
- KPIs analysieren: Bewerten Sie Leistungskennzahlen.
- Potenzial erkennen: Optimierungsmöglichkeiten ohne Risiko.
SYMESTIC steigert die Produktivität in über 20 Ländern, für Kunden wie Yanfeng, Eberspächer, Nidec und mehr.
Fazit: Cloud MES ist ein strategischer Gamechanger, der Kosten senkt, Effizienz steigert und die Fertigung zukunftssicher macht. Mit SYMESTIC gestalten Unternehmen die digitale Transformation erfolgreich.
Exklusives Whitepaper
Lernen Sie die modernsten Ansätze der Industrie 4.0, die Sie in Ihrer Produktion schon morgen umsetzen können, um innerhalb von 4 Wochen Ihre Kosten um gut 20% zu reduzieren.
mehr erfahren