10 decisive selection criteria for your new MES
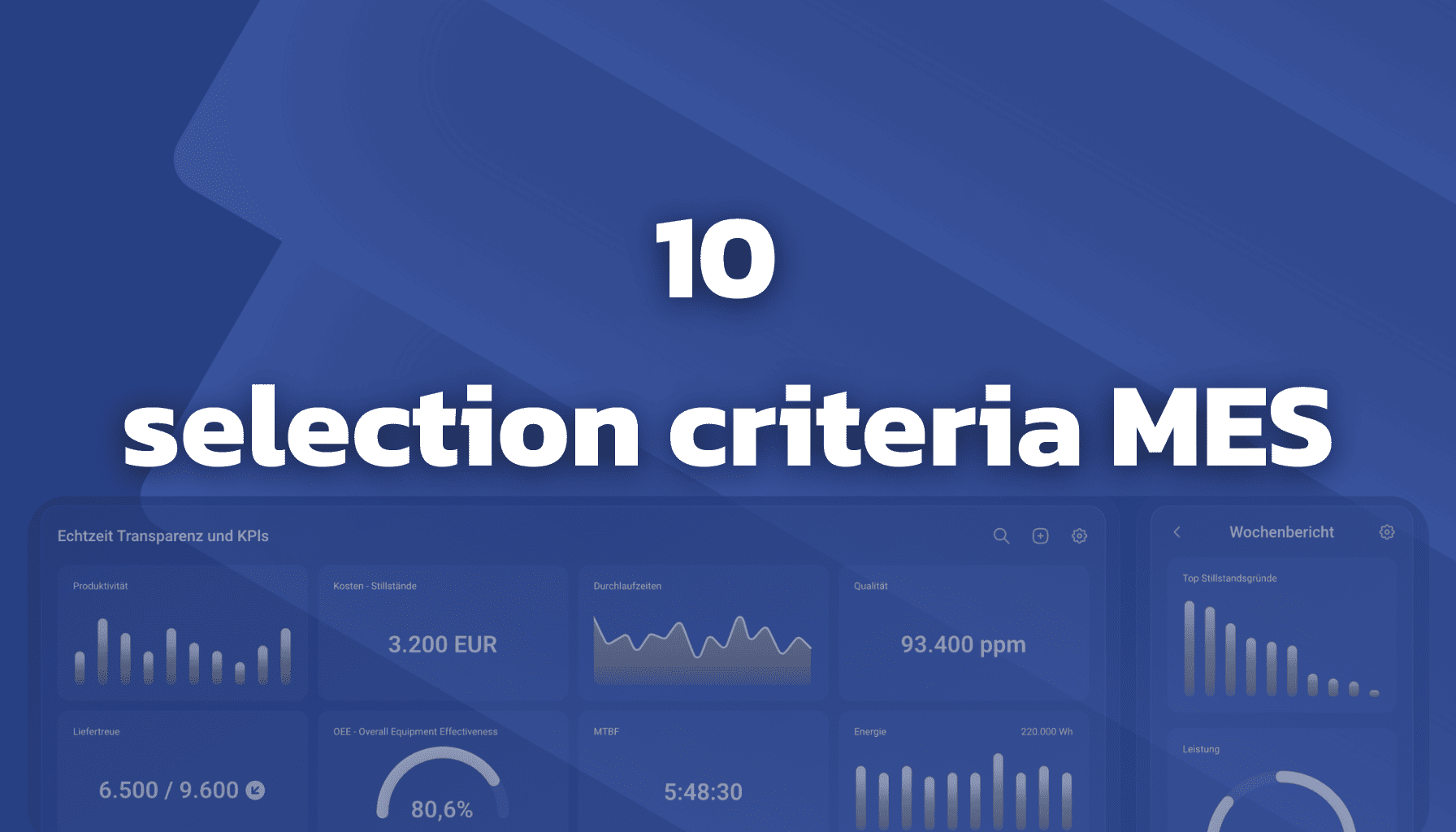
The Right MES Selection: Your Path to Digital Manufacturing
Implementing a Manufacturing Execution System (MES) is a pivotal step to enhance efficiency, transparency, and competitiveness in your production. But how do you choose the right solution? This guide outlines the ten key criteria for MES selection to ensure the best decision for your business.
Start Your MES Journey with SYMESTIC
Discover how SYMESTIC’s Cloud MES transforms your production in just 3 hours. Test real-time data and optimized processes—free and risk-free.
1. Implementation Time and Time-to-Value
Why It Matters
The time to productive use of an MES significantly impacts ROI. Traditional on-premises solutions often take 12–18 months, while modern Cloud MES can be operational in days or weeks.
What to Look For
- Project Timeline: Ask for specific implementation times for comparable projects.
- Phased Rollout: Can the system be implemented modularly for quick wins?
- Implementation Methodology: Agile approaches typically deliver faster results than waterfall methods.
Best Practice
Choose solutions with a rapid start—ideally delivering results within four weeks. Providers like SYMESTIC leverage pre-configured components for minimal time-to-value.
2. Flexibility and Scalability
Why It Matters
Businesses grow, diversify, or enter new markets. An MES must flexibly support these changes.
What to Look For
- Modular Design: Can features be added as needed?
- Capacity Limits: Are there restrictions on data volume, users, or connected machines?
- Global Scalability: Does the system support multiple sites and languages?
- Customizability: How easily can custom adjustments be made?
Best Practice
Cloud-native MES offer maximum flexibility and scalability. Review case studies of companies that scaled from a pilot plant to global rollout.
3. Seamless Integration and Connectivity
Why It Matters
An MES must communicate with machines (PLC, SCADA) and enterprise systems (ERP, PLM) to be effective.
What to Look For
- Standard Interfaces: Does the system support OPC UA, MQTT, or REST?
- ERP Integration: Are there connectors for common ERP systems?
- Legacy Integration: Can older machines be connected?
- Open API: Does the system allow custom integrations?
Best Practice
Select MES with diverse connectivity options. Edge gateways and protocols enable integration of modern and legacy equipment for seamless manufacturing digitalization.
4. User-Friendliness and Adoption
Why It Matters
An MES only reaches its full potential if used actively from shop floor to management. User-friendliness is key to adoption.
What to Look For
- Intuitive Interface: How quickly can new users navigate the system?
- Role-Based Views: Are there tailored interfaces for different user groups?
- Mobile Access: Is there an app or responsive web interface?
- Customizability: Can dashboards be configured without coding?
Best Practice
Test the system with end users. An intuitive MES like SYMESTIC, with a consumer-grade interface and mobile app, minimizes training efforts.
5. Total Cost of Ownership (TCO)
Why It Matters
The total cost of an MES goes beyond the purchase price, including implementation, customization, maintenance, and internal resources.
What to Look For
- Licensing Model: One-time costs or subscription? User- or machine-based pricing?
- Implementation Costs: What services are included?
- Internal Efforts: What resources do you need to provide?
- Upgrade Policy: Are updates included? How often are new versions released?
- Hardware Requirements: Do you need new infrastructure?
Best Practice
Create a TCO calculation over five years. SaaS solutions like SYMESTIC offer transparent costs and eliminate hardware and maintenance expenses.
Optimize Your MES Costs with SYMESTIC
With SYMESTIC’s Cloud MES, you save CAPEX and go live in 3 hours. Test it now for free!
6. Functionality and Specialization
Why It Matters
An MES must meet your industry-specific needs without compromising usability due to excessive complexity.
What to Look For
- Core Features: Does it cover production planning, quality, and material management?
- Industry Specialization: Does the provider have experience in your industry?
- Modular Design: Can you select only the needed features?
- Configurability: Can it be adapted without coding?
Best Practice
Prioritize your top 10 requirements. A modular MES like SYMESTIC allows starting with core features and expanding as needed.
7. Data Security and Compliance
Why It Matters
Production data is sensitive and must be protected. Compliance with regulations like GDPR is essential.
What to Look For
- Data Protection: How are data encrypted and secured?
- Hosting Options: Where are data stored? Do data centers meet your requirements?
- Access Controls: Are there granular permissions and audit trails?
- Certifications: Does the provider have security certifications (e.g., ISO 27001)?
- Regulatory Compliance: Does it support industry-specific regulations?
Best Practice
Conduct a security assessment. Cloud platforms like Microsoft Azure, used by SYMESTIC, offer robust data security and GDPR-compliant certifications.
8. Future-Proofing and Innovation
Why It Matters
An MES is a long-term investment. It must keep pace with rapid technological advancements.
What to Look For
- Development Roadmap: What is the system’s future plan?
- Innovation Cycle: How often are new features introduced?
- Technology Stack: Is it built on future-proof technologies?
- AI Capabilities: Does it offer AI features like predictive maintenance?
- Developer Ecosystem: Is there a partner network?
Best Practice
Evaluate the provider’s innovation track record. Cloud-native MES like SYMESTIC offer continuous updates and AI integration for future-proofing.
9. Support and Service
Why It Matters
An MES is business-critical. Issues must be resolved quickly and competently to avoid production downtime.
What to Look For
- Support Model: What support channels are available? Are there service levels?
- Response Times: How quickly are critical issues addressed?
- Availability: Is 24/7 support offered?
- Implementation Support: What assistance is provided during rollout?
- Training Offerings: What training is available for user groups?
Best Practice
Talk to existing customers about their support experiences. Providers like SYMESTIC offer not just technical support but also strategic guidance for manufacturing digitalization.
10. Vendor Stability and Partner Network
Why It Matters
An MES is a long-term investment. The vendor must be a reliable partner over time.
What to Look For
- Company Stability: How long has the vendor been in business? What is their financial health?
- Market Position: Is the vendor established or a newcomer?
- Partner Network: Are there implementation partners?
- Industry Experience: Does the vendor have expertise in your industry?
- Reference Customers: Are there successes with similar companies?
Best Practice
Visit reference customers. Vendors like SYMESTIC combine innovative Cloud MES with extensive experience and a strong partner network.
Secure Your MES Future with SYMESTIC
SYMESTIC’s Cloud MES ensures future-proof innovation and reliable support. Start your free 30-day trial today!
Conclusion: The Right Selection Process for Long-Term Success
MES selection is a complex but critical task. These ten criteria provide a clear framework to find the best solution for your manufacturing digitalization. Prioritize your needs—from rapid implementation to future-proofing—and consider cultural and organizational factors. Cloud-native MES like SYMESTIC excel in flexibility, cost, and innovation, while specialized vendors offer deep industry expertise.
“The right MES transforms your manufacturing sustainably—choose wisely!”
Begin Your MES Journey
With SYMESTIC’s Cloud MES, you go live in 3 hours, gaining instant transparency and efficiency. Experience the future of manufacturing with our free 30-day trial.
- Rapid Integration: Connect 1-2 machines.
- Real-Time Transparency: Analyze KPIs over 30 days.
- Risk-Free Testing: Unlock optimization without commitment.
SYMESTIC empowers global leaders like Yanfeng and Eberspächer across 20+ countries.
Conclusion: A structured selection process ensures the success of your MES selection. With SYMESTIC, shape the future of your manufacturing—efficient, secure, and innovative.