Shop Floor Management: The Ultimate Implementation Guide [2025]
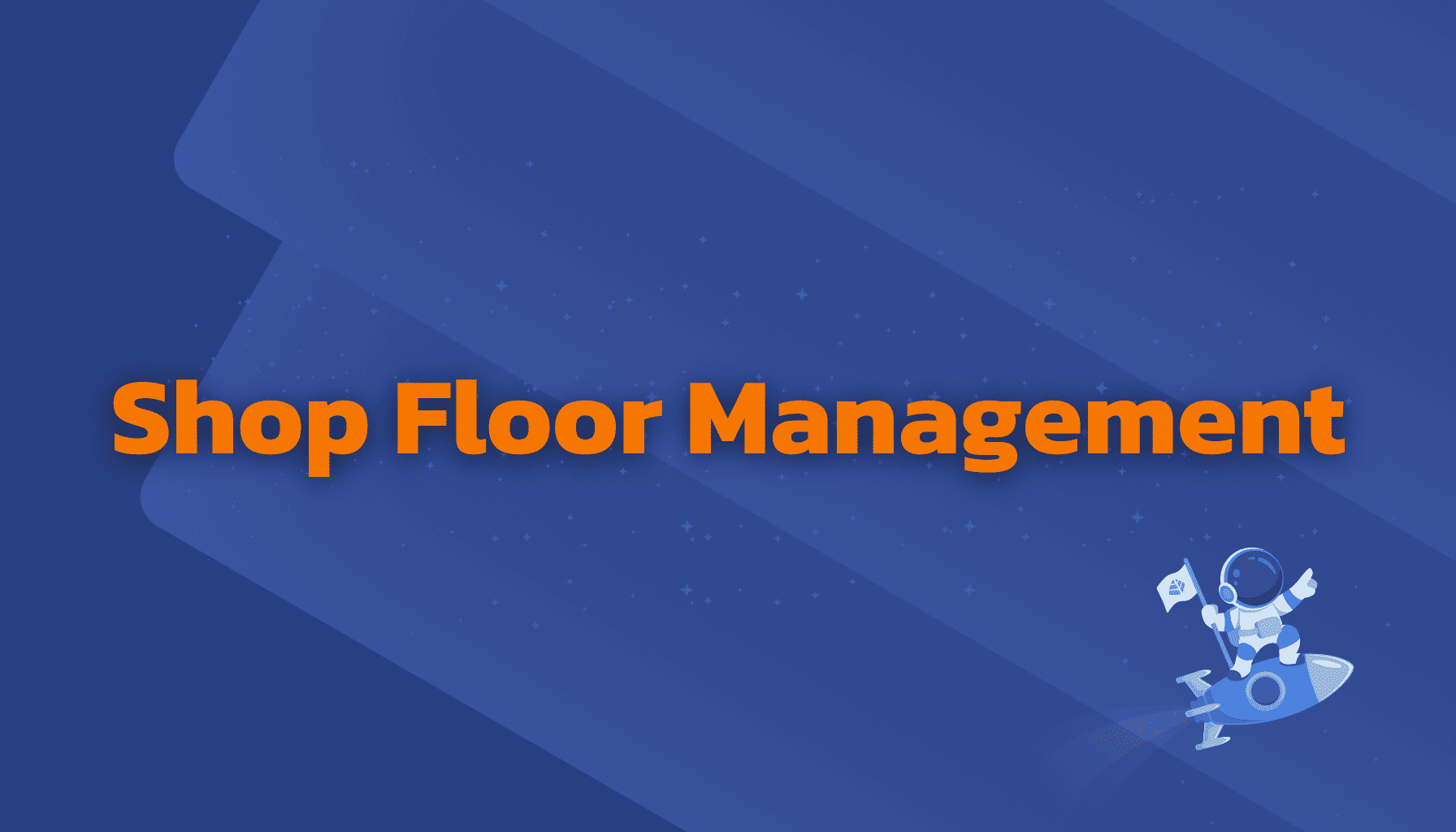
In this comprehensive guide, you'll learn everything you need to know about Shop Floor Management and how to effectively implement this leadership method in your organization. We will cover:
- How effective Shop Floor Management can increase productivity by up to 25%
- The 5 pillars critical for successful implementation
- How to avoid common pitfalls during implementation
- Proven strategies for daily execution
- Current trends and digital solutions for 2024
Fundamentals of Shop Floor Management
Shop Floor Management (SFM) is a practice-oriented leadership approach where managers are regularly and structurally present at the place of value creation. This systematic approach combines effective leadership with continuous process optimization and enables immediate response to production challenges.
Definition & Core Elements
The effectiveness of Shop Floor Management is based on three central core elements:
Leadership on Site
- Regular presence of managers in production
- Direct communication with employees
- Quick decision-making at the base level
Standardized Processes
- Structured shop floor meetings
- Defined escalation paths
- Systematic problem-solving routines
Visual Management
- Transparent display of key figures
- Real-time visualization of deviations
- Clear communication of objectives
History and Development
Shop Floor Management has its roots in the Toyota Production System of the 1950s. The Japanese concept of "Gemba" (実場, the real place) formed the basis for the modern management approach. Important development steps were:
- 1950s: Origin at Toyota as part of TPS
- 1980s: Adoption by Western companies
- 2000s: Integration of digital elements
- Today: Merger with Industry 4.0 concepts
Enhance Your Manufacturing with SYMESTIC
Connect your machines, gain real-time insights, and boost productivity by up to 20%. Join manufacturers across 20+ countries.
Significance in Modern Production
In today's manufacturing industry, Shop Floor Management plays a central role in increasing efficiency and quality. Companies that successfully implement SFM achieve on average:
- 20-30% higher productivity
- 15-25% fewer quality defects
- 40-60% shorter response times to problems
- Significantly higher employee satisfaction
Shop Floor Management is particularly valuable in times of increasing complexity:
- Flexibility: Quick adaptation to market requirements
- Transparency: Clear view of processes and metrics
- Efficiency: Optimized resource utilization
- Quality: Continuous improvement of product quality
The 5 Pillars of Shop Floor Management
The success of Shop Floor Management is based on five fundamental pillars that together form an effective leadership system:
1. Leadership on Site
The first and most important pillar involves active presence of leaders at the place of action:
- Regular shop floor walks by managers
- Direct communication with employees
- Immediate problem identification and solution
- On-site coaching and team support
Ideally, leaders spend 30-40% of their time directly in production to understand processes and identify improvement potential.
2. Visual Management
Visual management makes processes and performance transparent and immediately recognizable:
Shop Floor Management Boards
- Current metrics and KPIs
- Deviation analyses
- Action tracking
- Target agreements
Visualization Elements
- Color coding (e.g., traffic light system)
- Trend charts and diagrams
- Andon boards for fault reporting
- Digital dashboards
3. Standardized Communication
Effective communication follows clear structures in Shop Floor Management:
Daily Meetings
- Fixed times (usually at shift start)
- Defined participants
- Structured agenda
- Maximum duration of 15 minutes
Communication Cascade
- Level 1: Team leader meeting
- Level 2: Department manager meeting
- Level 3: Plant manager meeting
- Clearly defined escalation paths
Enhance Your Manufacturing with SYMESTIC
Connect your machines, gain real-time insights, and boost productivity by up to 20%. Join manufacturers across 20+ countries.
4. CIP & Problem Solving
Continuous improvement is firmly anchored in Shop Floor Management:
Systematic Problem Solving
- 8D methodology
- PDCA cycle
- A3 reporting
- Root Cause Analysis
Improvement Initiatives
- Employee suggestion system
- Kaizen events
- Quick-win implementation
- Long-term optimization projects
5. Employee Involvement
Active participation of all employees is crucial for success:
Empowerment
- Transfer of responsibility
- On-site decision-making authority
- Training and development
- Recognition of achievements
Teamwork
- Cross-functional collaboration
- Joint goal setting
- Regular exchange of experiences
- Collegial learning
The successful integration of these five pillars leads to:
- 25-35% higher productivity
- 40-50% shorter throughput times
- 60-70% reduced problem-solving times
- Significantly increased employee motivation
Practical Implementation
The successful introduction of Shop Floor Management requires a structured approach and the right combination of people, methods, and tools. What's crucial is not theoretical perfection but practical applicability in everyday business operations.
Shop Floor Management Boards
Shop floor boards are the heart of visual management. They serve as a central communication point and visualize all important information at a glance. While traditionally physical boards are used, modern digital boards offer significant advantages:
- Automatic real-time updates
- Site-wide access
- Simplified historical data analysis
- Combination of physical and digital boards for optimal results
Daily Routines & Meetings
Success is based on clearly structured routines:
- 5-10 minute daily shift-start meetings
- Weekly reviews for trend analysis
- Regular schedule and structure
- Focus on continuous improvement
Key Figures & KPIs
Selection of the right metrics is crucial:
- Focus on essential indicators
- Classic production metrics (OEE, quality rate, throughput time)
- Gradual expansion of basic KPIs
- Automated data collection through digitalization
Best Practices & Success Factors
Successful Examples from Practice
A medium-sized automotive supplier achieved impressive results:
- 30% productivity increase within 6 months
- 45% reduction in throughput times
- 25% quality improvement
- ROI after 4 months
- Typical Challenges
Common challenges include:
Cultural Barriers
- Resistance to change
- Need for new thinking patterns
- Emphasis on transparency
Technical Obstacles
- Insufficient data quality
- Time-consuming manual data collection
- Lack of system integration
- Inconsistent metrics
Organizational Problems
- Integration with existing processes
- Coordination between departments and shifts
Proven Solution Approaches
Successful companies rely on:
Clear Leadership Responsibility
- Active management support
- Regular shop floor presence
- Participation in meetings
Systematic Employee Development
- Comprehensive training program
- Special leadership training
- Practical problem-solving workshops
- Regular refresher courses
Digital Support
- Cloud-based solutions
- Automatic data collection
- Site-wide transparency
- Easy scalability
ROI & Added Value
Typical improvements after successful implementation:
Short-term (3-6 months)
- 15-20% higher productivity
- 30-40% fewer unplanned downtimes
- Improved employee motivation
Long-term (12+ months)
- 25-35% cost savings
- 40-50% shorter throughput times
- Sustainable quality improvement
Integration with Other Management Methods
Shop Floor Management works effectively with:
- Lean Management
- Kaizen approach
- Six Sigma
- Industry 4.0 concepts
Enhance Your Manufacturing with SYMESTIC
Connect your machines, gain real-time insights, and boost productivity by up to 20%. Join manufacturers across 20+ countries.
The Future of Shop Floor Management
Future developments include:
- Digital transformation integration
- AI and Machine Learning applications
- Predictive Analytics
- Smart Factory integration
- Mobile technologies
- Continued focus on human interaction
Conclusion
Shop Floor Management continues to evolve while remaining an indispensable tool for manufacturing companies. Success lies in balancing proven methods with innovative digital solutions. Companies that find this balance create the best conditions for successful and sustainable production optimization.