What does digitalization mean in production?
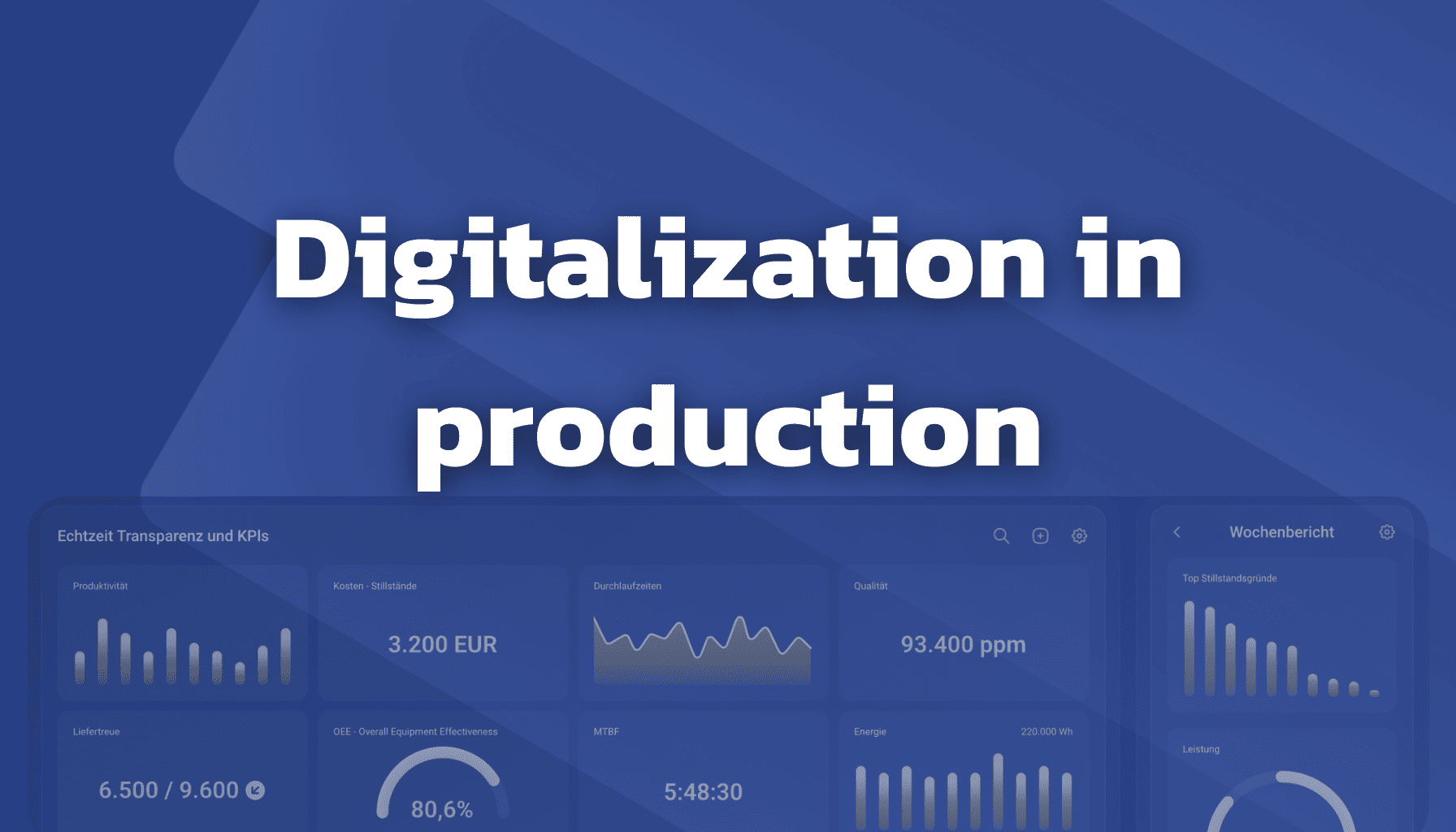
Table of Contents
- What Is Manufacturing Digitalization?
- The Evolution of Manufacturing Digitalization
- Transformative Benefits of Manufacturing Digitalization
- Digitalization and Human-Machine Collaboration
- Core Elements of Digitalized Manufacturing
- The Path to Digitalized Manufacturing
- The Role of Cloud MES in Digitalized Manufacturing
- Challenges of Manufacturing Digitalization
- The Future of Digitalized Manufacturing
- SYMESTIC: Revolutionary Cloud MES Solution
Definition
Manufacturing digitalization refers to the use of connected, digital, and automated technologies in production processes. It bridges the physical and digital worlds, enabling transparency, process optimization, and innovative business models.
Digitalization involves capturing, structuring, and analyzing data while connecting machines, processes, and products through advanced technologies. It forms the foundation for Industry 4.0, distinguishing itself from automation by providing comprehensive connectivity and intelligent control across the entire production system—from shop floor to top floor.
Manufacturing digitalization has evolved through distinct phases:
- Conventional Automation: Individual machines automated but operating in isolation.
- Computer-Aided Systems: Introduction of CAD/CAM and computer-controlled processes.
- Connected Systems: Machines communicate via local networks.
- Cloud-Based Solutions: Centralized data storage enables cross-site collaboration.
- Cloud-Native Systems: Built for the cloud, offering unmatched flexibility.
Modern manufacturers are transitioning to cloud-native systems, serving as the digital backbone for production.
1. Boosted Efficiency and Cost Reduction
Digitalization enhances efficiency by:
- Reducing Downtime: Real-time monitoring minimizes unplanned outages.
- Optimizing Resources: Efficient use of materials and energy.
- Automating Processes: Digital workflows replace manual tasks.
- Shortening Lead Times: Streamlined planning accelerates production.
Cloud-based MES systems can achieve 10-25% higher overall equipment effectiveness (OEE) and 30-60% less scrap.
2. Maximum Transparency with Real-Time Data
Digitalized manufacturing delivers:
- Real-Time Monitoring: Continuous tracking of KPIs.
- Data-Driven Decisions: Precise data over intuition.
- Early Warning Systems: Automatic issue detection.
- Traceability: Seamless documentation.
3. Enhanced Flexibility and Agility
Flexibility becomes a competitive edge through:
- Rapid Product Changes: Quick changeovers.
- Customized Production: Lot-size-one becomes viable.
- Scalability: Adapt to fluctuating demand.
- Dynamic Planning: Instant adjustments.
4. Improved Quality and Customer Satisfaction
Digitalization elevates quality by:
- Integrated Quality Checks: Continuous monitoring.
- Statistical Process Control: Early deviation detection.
- Error Prevention: Digital assistance systems.
- Consistent Processes: Standardized workflows.
Summary: Manufacturing digitalization delivers transformative benefits, from efficiency gains to enhanced quality, empowering businesses to thrive.
Digitalization fosters human-centric production:
- Eliminating Repetitive Tasks: Automation handles monotonous work.
- New Roles: Workers focus on planning and optimization.
- Digital Assistance: Contextual information supports employees.
- Collaborative Robotics: Humans and robots work together.
Modern MES systems enhance productivity with intuitive interfaces and timely data delivery.
1. Connected Machines and Systems (IIoT)
The Industrial Internet of Things (IIoT) includes:
- Sensors: Continuous data collection.
- Connectivity: Machine-to-machine communication.
- Edge Computing: Decentralized data processing.
- Retrofitting: Upgrading legacy machines.
2. Manufacturing Execution Systems (MES)
An MES connects planning and production:
- Production Planning: Optimal resource use.
- Material Management: Streamlined material flow.
- Quality Management: Integrated controls.
- Workforce Management: Skill-based planning.
3. Data Analytics and Artificial Intelligence
Intelligent data use through:
- Descriptive Analytics: Performance transparency.
- Diagnostic Analytics: Root cause identification.
- Predictive Analytics: Forecasting issues.
- Prescriptive Analytics: Optimal action recommendations.
Test Digitalization with SYMESTIC
Discover the benefits of digitalized manufacturing with our free 30-day SYMESTIC trial. Start with real-time data, optimized processes, and transparent KPIs—risk-free.
Implementing digitalization requires a strategic approach:
1. Analysis and Strategy
- Assess current processes and pain points.
- Develop a digitalization strategy with clear goals.
- Identify high-ROI use cases.
- Select suitable technologies.
2. Piloting and Quick Wins
- Start with a single line or process.
- Implement core functionalities.
- Showcase early successes.
- Learn from feedback.
3. Scaling and Integration
- Roll out successes to other areas.
- Integrate with existing systems like ERP and PLM.
- Drive change management.
- Continuously optimize processes.
A cloud-native MES is the backbone of digitalized manufacturing, connecting machines, processes, and people.
- Rapid Deployment: Ready in days.
- Maximum Flexibility: Modular customization.
- Scalability: Effortless expansion.
- Continuous Innovation: Automatic updates.
- High Security: Robust architecture.
Investments typically pay off within 3-12 months, far faster than on-premises solutions.
Summary: Cloud MES drives digital transformation with speed, flexibility, and security, enabling manufacturers to stay ahead.
Unlock the Power of Cloud MES
Experience the future of manufacturing with SYMESTIC’s free 30-day Cloud MES trial. Transform your operations with real-time insights and seamless integration.
1. Data Security and Sovereignty
- Challenge: Concerns over sensitive data in the cloud.
- Solution: Robust security protocols and encryption.
2. Integration of Existing Machines and Systems
- Challenge: Legacy machines lack modern interfaces.
- Solution: Edge gateways and IoT sensors for retrofitting.
3. Employee Acceptance and Skills
- Challenge: Resistance to change and lack of digital skills.
- Solution: Early engagement, training, and user-friendly interfaces.
4. Internet Reliability and Offline Capability
- Challenge: Downtime risks due to internet disruptions.
- Solution: Redundant connections, edge computing, and offline functionality.
Summary: Targeted solutions like security frameworks, retrofitting, and training address common digitalization challenges, ensuring a smooth transition.
Manufacturing digitalization is advancing with cutting-edge trends:
1. Artificial Intelligence and Machine Learning
- Predictive Maintenance: Anticipating equipment failures.
- Autonomous Planning: AI-optimized production sequences.
- Quality Prediction: Forecasting quality issues.
2. Digital Twins and Simulation
- Virtual Commissioning: Testing before implementation.
- Real-Time Optimization: Adjustments via simulations.
- Scenario Planning: What-if analyses.
3. Augmented and Virtual Reality
- AR-Guided Maintenance: Visual step-by-step instructions.
- VR Training: Immersive skill-building in virtual environments.
- Digital Work Instructions: Interactive, real-time guidance.
Summary: AI, digital twins, and AR/VR are revolutionizing manufacturing with predictive insights, simulations, and immersive training.
SYMESTIC sets the standard with its cloud-native MES, integrating all tools needed for digital transformation:
- Modular Design: Flexible modules for MDE, BDE, and AI analytics.
- Fast Deployment: Operational in days.
- Seamless Integration: Connects modern and legacy systems.
- Intuitive Interface: User-friendly dashboards.
SYMESTIC empowers global manufacturers with proven results in efficiency, quality, and cost savings.
Summary: SYMESTIC’s scalable, flexible Cloud MES drives digital success for manufacturers worldwide.
Conclusion: Digitalization as the Key to Success
Manufacturing digitalization is critical for staying competitive. It delivers transformative benefits:
- Efficiency Gains: Reduced downtime and faster cycles.
- Transparency: Real-time data for informed decisions.
- Flexibility: Adapting to market demands.
- Quality: Fewer errors, higher customer satisfaction.
“Those who don’t digitalize today won’t compete tomorrow.”
Test Cloud MES for Free
Discover the power of Cloud MES with SYMESTIC’s free 30-day trial. Connect machines, gain real-time insights, and unlock optimization potential—without risk.
- Easy Integration: Connect 1-2 machines.
- Real-Time Data: Collect data for 30 days.
- Analyze KPIs: Evaluate performance metrics.
- Unlock Potential: Identify improvements risk-free.
SYMESTIC boosts productivity for global leaders like Yanfeng, Eberspächer, Nidec, and more across 20+ countries.
Conclusion: Cloud MES is a game-changer, cutting costs, boosting efficiency, and future-proofing manufacturing. SYMESTIC leads the way in digital transformation.
-right: 8px;">- Challenge: Legacy machines lack modern interfaces.
- Solution: Edge gateways and IoT sensors for retrofitting.
3. Employee Acceptance and Skills
- Challenge: Resistance to change and lack of digital skills.
- Solution: Early engagement, training, and user-friendly interfaces.
4. Internet Reliability and Offline Capability
- Challenge: Downtime risks due to internet disruptions.
- Solution: Redundant connections, edge computing, and offline functionality.
Summary: Targeted solutions like security frameworks, retrofitting, and training address common digitalization challenges, ensuring a smooth transition.
Manufacturing digitalization is advancing with cutting-edge trends:
1. Artificial Intelligence and Machine Learning
- Predictive Maintenance: Anticipating equipment failures.
- Autonomous Planning: AI-optimized production sequences.
- Quality Prediction: Forecasting quality issues.
2. Digital Twins and Simulation
- Virtual Commissioning: Testing before implementation.
- Real-Time Optimization: Adjustments via simulations.
- Scenario Planning: What-if analyses.
3. Augmented and Virtual Reality
- AR-Guided Maintenance: Visual step-by-step instructions.
- VR Training: Immersive skill-building in virtual environments.
- Digital Work Instructions: Interactive, real-time guidance.
Summary: AI, digital twins, and AR/VR are revolutionizing manufacturing with predictive insights, simulations, and immersive training.
SYMESTIC sets the standard with its cloud-native MES, integrating all tools needed for digital transformation:
- Modular Design: Flexible modules for MDE, BDE, and AI analytics.
- Fast Deployment: Operational in days.
- Seamless Integration: Connects modern and legacy systems.
- Intuitive Interface: User-friendly dashboards.
SYMESTIC empowers global manufacturers with proven results in efficiency, quality, and cost savings.
Summary: SYMESTIC’s scalable, flexible Cloud MES drives digital success for manufacturers worldwide.
Conclusion: Digitalization as the Key to Success
Manufacturing digitalization is critical for staying competitive. It delivers transformative benefits:
- Efficiency Gains: Reduced downtime and faster cycles.
- Transparency: Real-time data for informed decisions.
- Flexibility: Adapting to market demands.
- Quality: Fewer errors, higher customer satisfaction.
“Those who don’t digitalize today won’t compete tomorrow.”
Test Cloud MES for Free
Discover the power of Cloud MES with SYMESTIC’s free 30-day trial. Connect machines, gain real-time insights, and unlock optimization potential—without risk.
- Easy Integration: Connect 1-2 machines.
- Real-Time Data: Collect data for 30 days.
- Analyze KPIs: Evaluate performance metrics.
- Unlock Potential: Identify improvements risk-free.
SYMESTIC boosts productivity for global leaders like Yanfeng, Eberspächer, Nidec, and more across 20+ countries.
Conclusion: Cloud MES is a game-changer, cutting costs, boosting efficiency, and future-proofing manufacturing. SYMESTIC leads the way in digital transformation.