Work in Progress (WIP)
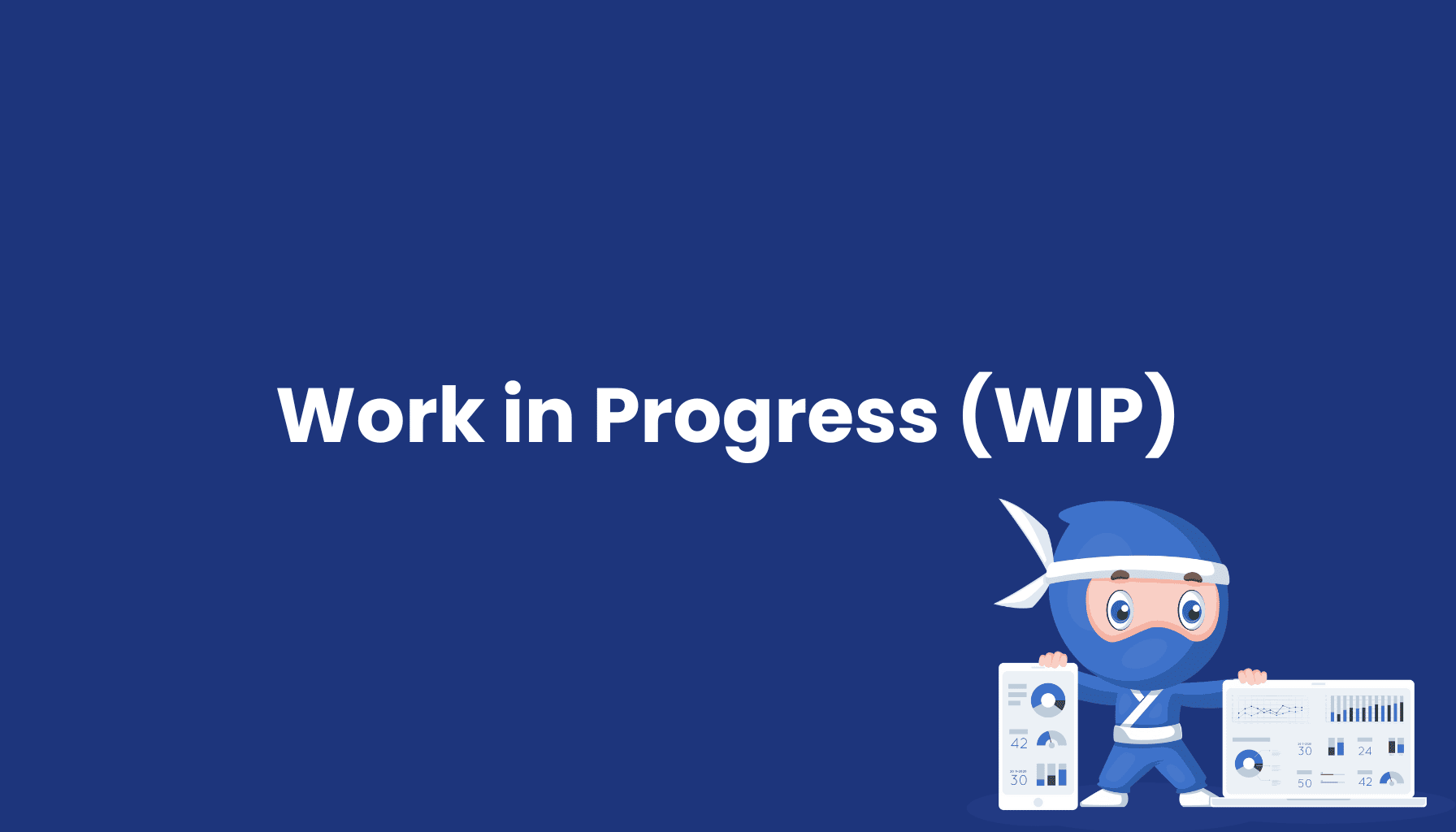
What is Work in Progress (WIP)?
Work in Progress (WIP) refers to the amount of unfinished products currently in the production process. WIP includes all materials, labor, and costs invested in production that are not yet considered finished products. Monitoring and optimizing WIP is crucial for increasing efficiency and reducing production costs.
Importance and Optimization of WIP
Excessive WIP can lead to high storage costs, prolonged lead times, and slowed production flow. Effectively managing WIP helps maximize productivity and streamline material flow, minimizing capital tied up in unfinished products and making production processes more efficient.
Benefits of WIP Optimization
- Cost Savings: Reduced inventory and capital tied up in unfinished products lead to lower storage and operating costs.
- Accelerated Production Flow: Lower WIP levels reduce bottlenecks and improve material flow, which shortens lead times.
- Improved Inventory Management: Enhanced transparency and control over production status allow for better inventory planning.
Strategies for WIP Optimization
-
Lean Manufacturing: Applying Lean principles reduces waste in production and optimizes workflows. Methods like 5S and Value Stream Mapping help minimize bottlenecks and unnecessary inventory.
-
Just-in-Time (JIT) Production: Producing only what is needed when it is needed minimizes inventory and streamlines production processes.
-
Continuous Improvement (Kaizen): The Kaizen philosophy encourages regular process improvements, systematically identifying and eliminating bottlenecks.
-
Use of ERP Systems: Modern ERP software enables real-time monitoring and management of WIP levels, supporting accurate inventory management and production planning.
Conclusion
Efficient management and optimization of Work in Progress (WIP) are vital for reducing production costs and improving workflow. By applying Lean Manufacturing, Just-in-Time production, and continuous improvement, companies can effectively reduce WIP levels. ERP systems are essential tools for real-time production monitoring and precise inventory control. Optimizing WIP management thus significantly contributes to increased efficiency and competitiveness.