Six Sigma
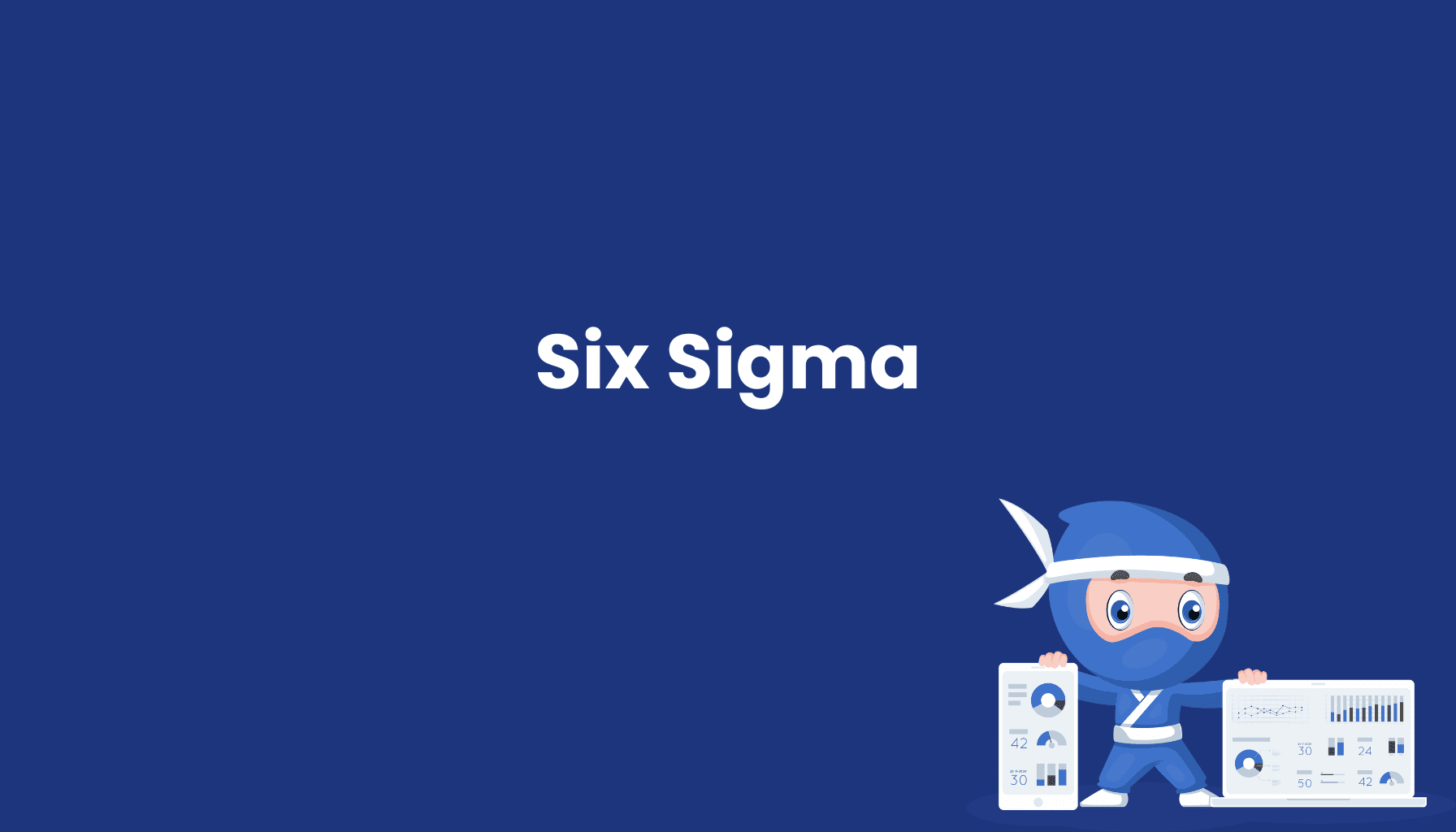
What is Six Sigma?
Six Sigma is a data-driven approach and methodology for improving the quality and efficiency of processes. Originally developed by Motorola in the 1980s, Six Sigma aims to minimize the number of defects in processes by keeping them within six standard deviations (sigma) from the mean, which equates to a defect rate of 3.4 defects per million opportunities.
Benefits of Six Sigma
- Quality Improvement: By reducing the defect rate, the quality of products or services is significantly enhanced.
- Cost Reduction: Defects and errors incur costs. Minimizing them can lead to substantial cost savings.
- Customer Satisfaction: Higher quality and lower defect rates result in more satisfied customers.
- Efficiency Enhancement: Optimized processes lead to better resource utilization and more efficient operations.
Methods and Tools of Six Sigma
Six Sigma employs a combination of statistical methods and quality management tools. Key tools and methods include:
- Statistical Process Control (SPC): Monitoring and controlling processes using statistical methods.
- Failure Mode and Effects Analysis (FMEA): Identifying and analyzing potential failures in a process or product.
- Regression Analysis: Investigating the relationships between variables to identify causes of problems.
- Hypothesis Testing: Testing assumptions and hypotheses about the process.
DMAIC Cycle
The DMAIC Cycle is a core component of Six Sigma, used to improve existing processes. It consists of five phases:
- Define: Define the project and goals, identify customer requirements.
- Measure: Collect data and measure current process performance.
- Analyze: Analyze the data to identify root causes of defects and variations.
- Improve: Develop and implement solutions to improve the process.
- Control: Monitor the improved process to ensure the improvements are sustained.
DMADV Cycle
The DMADV Cycle is used for developing new processes or products and also consists of five phases:
- Define: Define project goals and requirements.
- Measure: Gather relevant data and specifications.
- Analyze: Analyze the data to develop design options.
- Design: Develop the detailed design for the new process or product.
- Verify: Verify and validate the design to ensure it meets the requirements.
Conclusion
Six Sigma is a powerful tool for enhancing quality and efficiency in businesses. By applying statistical methods and quality management tools, and using the DMAIC and DMADV cycles, companies can optimize their processes, reduce costs, and increase customer satisfaction. Continuous improvement and control of processes ensure that the achieved improvements are maintained.