Quality Costs
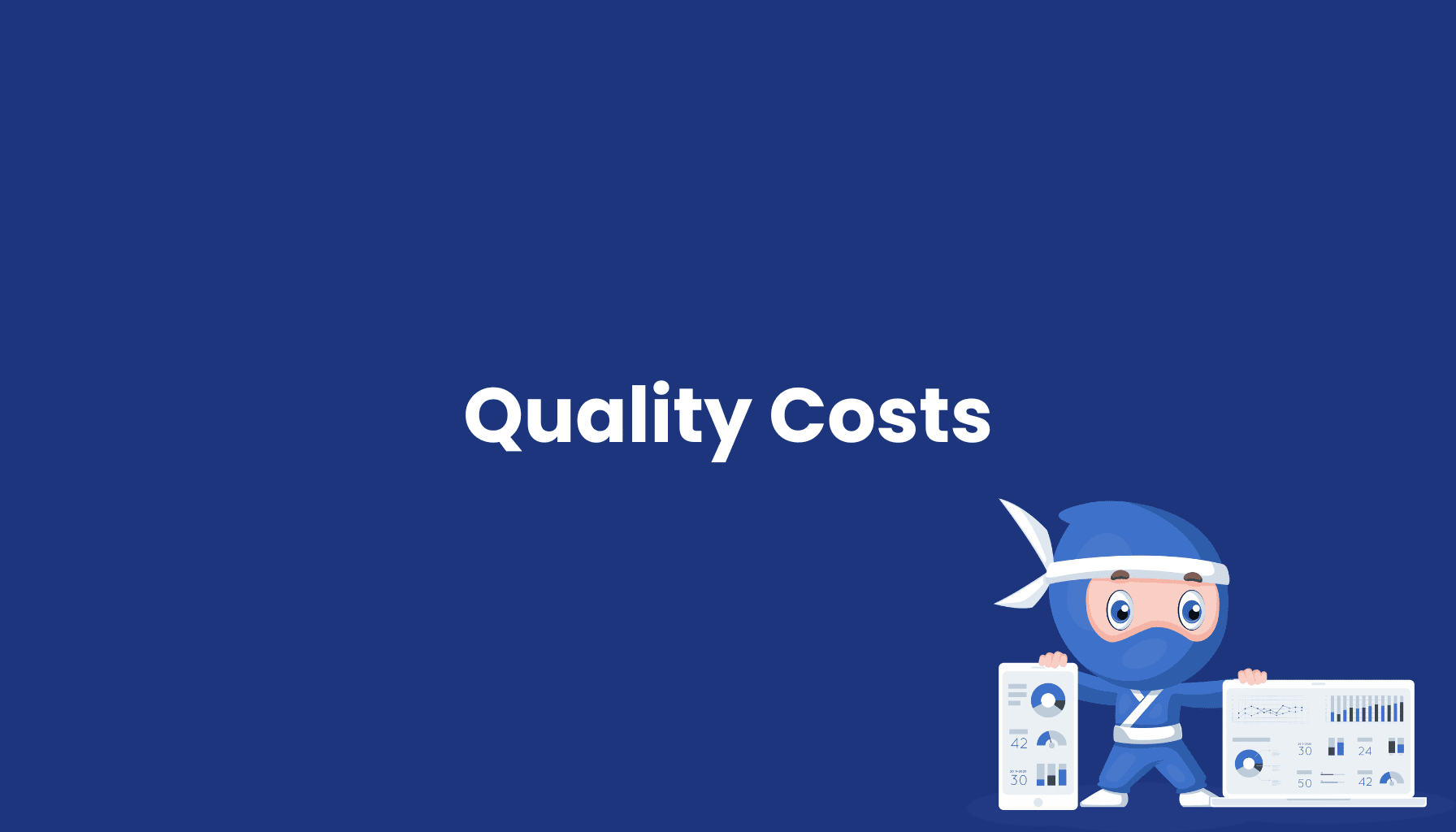
What Are Quality Costs?
Quality costs encompass the total expenditures associated with ensuring and improving product quality. The systematic collection and analysis of these costs serve as a fundamental basis for strategic quality decisions.
Systematic Cost Structure
Quality costs are divided into three fundamental categories:
Prevention Costs
Expenses incurred to prevent defects before production:
- Quality planning expenses: Developing standards and specifications.
- Process validations: Approving and verifying manufacturing processes.
- Employee training: Enhancing qualifications for quality processes.
- Preventive maintenance: Ensuring equipment reliability to avoid failures.
- Quality system implementation: Establishing and maintaining quality management systems.
Appraisal Costs
Costs associated with verifying and ensuring quality standards:
- Incoming goods inspection: Checking raw materials and components.
- Process inspections: Monitoring production processes.
- Final inspections: Quality control before delivery.
- Inspection equipment monitoring: Calibration and maintenance of measuring tools.
- Laboratory testing: Performing quality checks under controlled conditions.
Failure Costs
Costs resulting from defects in products or processes:
- Internal rework: Fixing defects before delivery.
- Scrap costs: Losses due to unusable products.
- External complaints: Handling customer claims and complaints.
- Warranty services: Costs of repairs or replacements.
- Reputation damage: Long-term effects on brand image.
Implementation Framework
Systematic collection and analysis of quality costs involve:
- Defining relevant cost centers: Allocating specific quality costs to departments or processes.
- Establishing collection systems: Implementing tools for recording costs.
- Utilizing analytical tools: Employing software and methods for in-depth evaluation.
- Developing optimization strategies: Planning and executing cost reduction measures.
- Continuous monitoring: Tracking and adapting strategies based on real-time data.
Performance Metrics
Quantitative evaluation of quality costs includes:
- Cost of Poor Quality (COPQ): Calculating costs arising from defects and failures.
- Quality Cost Ratio: Assessing the relationship between quality costs and overall production costs.
- Prevention-to-Failure Cost Ratio: Comparing investments in prevention versus failure costs.
- Return on Quality Investment (ROQI): Measuring the financial benefits of quality improvements.
- Quality-related productivity indicators: Evaluating the efficiency of quality initiatives.
Optimization Strategies
Effective reduction of quality costs can be achieved through:
- Enhancing preventive measures: Prioritizing defect prevention over correction.
- Process optimization: Streamlining workflows to minimize errors.
- Automated quality control: Leveraging technology for real-time monitoring.
- Employee qualification: Training staff to ensure adherence to quality standards.
- Continuous improvement: Applying methods like Kaizen or Six Sigma for ongoing quality enhancement.