The Kaizen philosophy: A guide to continuous improvement
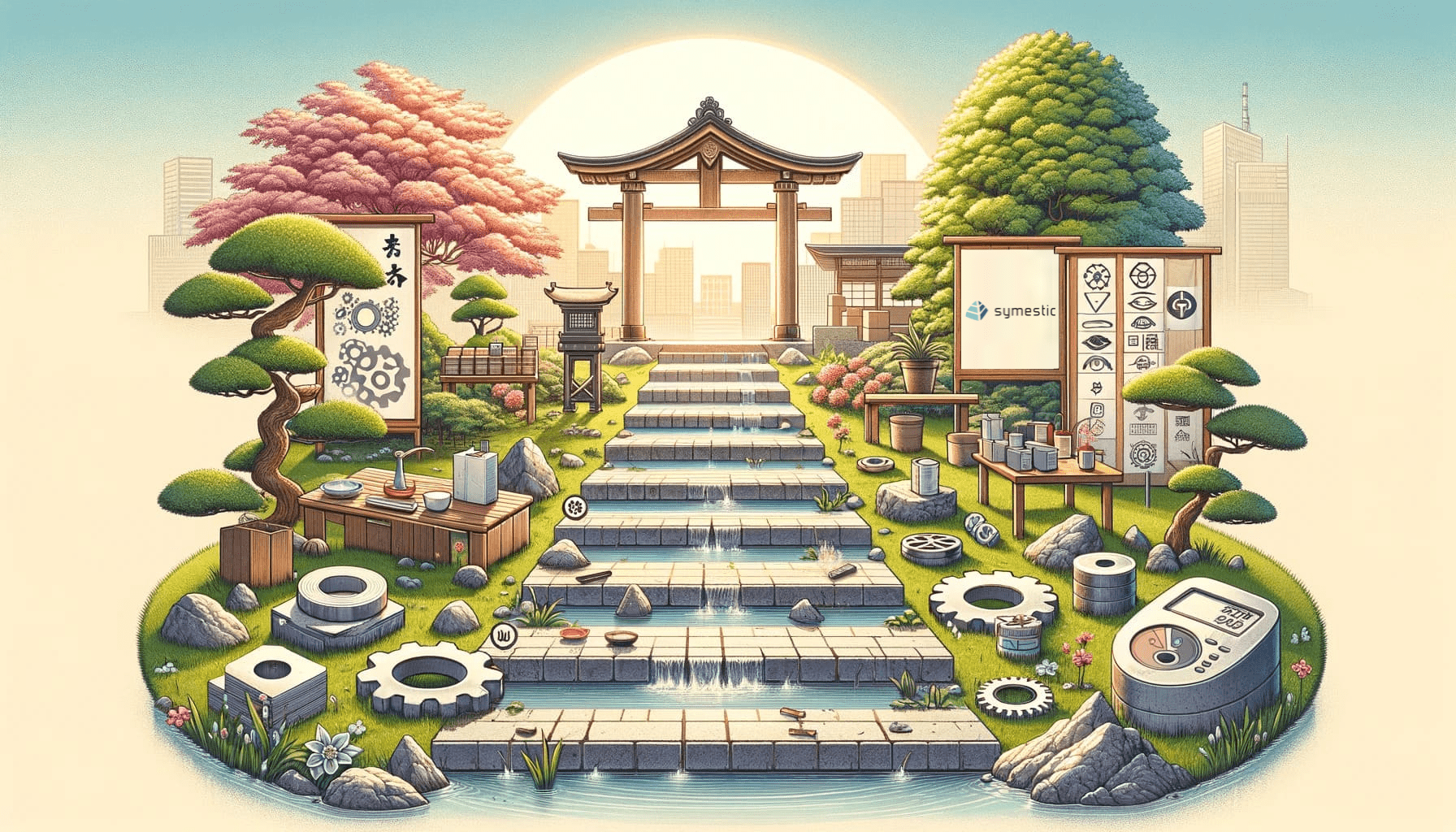
What is Kaizen? A Guide to Continuous Improvement
Kaizen, a Japanese term meaning "change for the better," is a philosophy of continuous improvement through small, incremental changes. It focuses on enhancing a company’s efficiency and effectiveness by regularly refining processes, products, and systems. Unlike large-scale overhauls, Kaizen minimizes disruptions while driving significant long-term improvements, making it a cornerstone of modern business strategies.
Amplify Your Kaizen Journey with Symestic
Turn Kaizen’s continuous improvement into measurable success with Symestic Cloud MES – gain real-time insights, optimize processes, and drive efficiency with data-driven precision. Kickstart your journey with a 30-day free trial!
Transform your processes with Symestic – full support included.
Table of Contents
Use this guide as an introduction to the world of Kaizen and learn how to establish a culture of continuous improvement in your production processes. Let’s get started!
The Origin of the Kaizen Method: A Historical Perspective
Kaizen emerged in the 1940s in Japan as part of post-war quality circles, initially adopted by Toyota to prevent defects in manufacturing. The philosophy gained global recognition in 1986 with Masaaki Imai’s book, "Kaizen: The Key to Success in Competition", which introduced the concept to Western businesses.
Today, Kaizen is applied across diverse industries, including healthcare, service sectors, education, retail, and hospitality, driving efficiency and customer satisfaction.
Core Principles of the Kaizen Method
The Kaizen philosophy is built on key principles that foster a culture of continuous improvement and collaboration within organizations.
Kaizen Principles at a Glance
Continuous Improvement
Involve Everyone
Customer Needs
Data-Driven
Quality First
Core principles driving Kaizen’s continuous improvement culture
Continuous Improvement
The Kaizen principle of continuous improvement (CIP) focuses on gradual enhancements to processes, products, or services. This ensures organizations consistently strive for better efficiency and quality, staying competitive through small, impactful changes.
Involve Everyone
Kaizen encourages all employees to take responsibility for improvement. By empowering everyone to contribute, it fosters collaboration, smoother operations, and a shared sense of ownership in achieving organizational goals.
Understand Customer Needs
Understanding customer needs allows companies to prioritize improvements that deliver the most value, ensuring efforts align with what matters most to their audience.
Data-Driven Approaches
Kaizen relies on data to make objective decisions, ensuring consistency across teams and departments. This approach minimizes subjective errors and maximizes improvement outcomes.
Quality Takes Precedence
Quality is at the heart of Kaizen, extending beyond the end product to all processes and systems. Prioritizing quality at every stage enhances customer satisfaction, fosters loyalty, and ensures long-term success.
Goals of the Kaizen Method: Driving Continuous Improvement
The primary goal of Kaizen is to achieve continuous improvement across all aspects of a company’s operations through small, incremental changes. This involves identifying inefficiencies, developing solutions, testing them, and refining based on feedback.
Kaizen also promotes employee engagement by encouraging everyone to contribute ideas, which boosts morale, enhances productivity, and fosters a culture of collaboration.
Tools and Methods of Kaizen: Practical Approaches
The 5S Method in the Context of Kaizen
The 5S method is a workplace organization system that aligns with Kaizen by streamlining processes and increasing efficiency. It consists of five steps:
- Seiri (Organizing): Sort and remove unnecessary items from the workplace.
- Seiton (Orderliness): Arrange tools and materials for easy access.
- Seiso (Cleanliness): Maintain a clean and safe workspace to enhance quality.
- Seiketsu (Personal Discipline): Standardize processes to ensure consistency.
- Shitsuke (Discipline): Foster a culture of discipline to sustain improvements.
By organizing the workplace and maintaining discipline, the 5S method enhances safety, reduces waste, and supports Kaizen’s goal of continuous improvement.
The PDCA Cycle as a Core Kaizen Tool
The PDCA cycle (Plan-Do-Check-Act), also known as the Deming Cycle, is a fundamental Kaizen tool for continuous improvement. It provides a structured feedback loop to refine processes iteratively.
The PDCA Cycle in Kaizen
Set Goals
Analyze & Plan
Execute
Implement Plan
Analyze
Review Results
Adjust
Implement Changes
The PDCA cycle consists of four steps:
- Plan: Set goals, analyze data, and create an action plan to address inefficiencies.
- Do: Execute the plan and collect data to track progress and performance.
- Check: Analyze results, compare against goals, and assess the effectiveness of the plan.
- Act: Implement changes based on findings, refining processes for better outcomes.
The Standardize-Do-Check-Act (SDCA) cycle extends PDCA by emphasizing the standardization of processes. After standardizing, companies use data to monitor progress and implement further improvements, reinforcing a culture of continuous enhancement.
Criticism of the Kaizen Philosophy: Challenges and Limitations
While Kaizen is widely praised for its focus on continuous improvement, it faces some criticism.
- Critics argue that Kaizen’s incremental approach may lead to many small improvements but lacks the potential for revolutionary innovation.
- Maintaining focus on improvements amidst daily business pressures, such as deadlines, can be challenging.
- Some believe an overemphasis on small changes may cause companies to miss opportunities for transformative breakthroughs.
Differences and Advantages of Kaizen Over Other Management Concepts
Kaizen differs from other management methods like Six Sigma in several key ways.
- Kaizen focuses on small, incremental improvements, while Six Sigma often involves large-scale process overhauls.
- It promotes collaboration at all employee levels, unlike top-down approaches in other methods.
- Kaizen emphasizes testing and refining solutions, ensuring thoughtful implementation over rapid deployment.
These differences make Kaizen a unique approach for fostering a sustainable culture of continuous improvement, driving long-term efficiency and engagement.
Summary: Kaizen drives continuous improvement through small changes, empowering employees and enhancing efficiency across industries.