Lean Production: Definition, Methoden & Praxisleitfaden
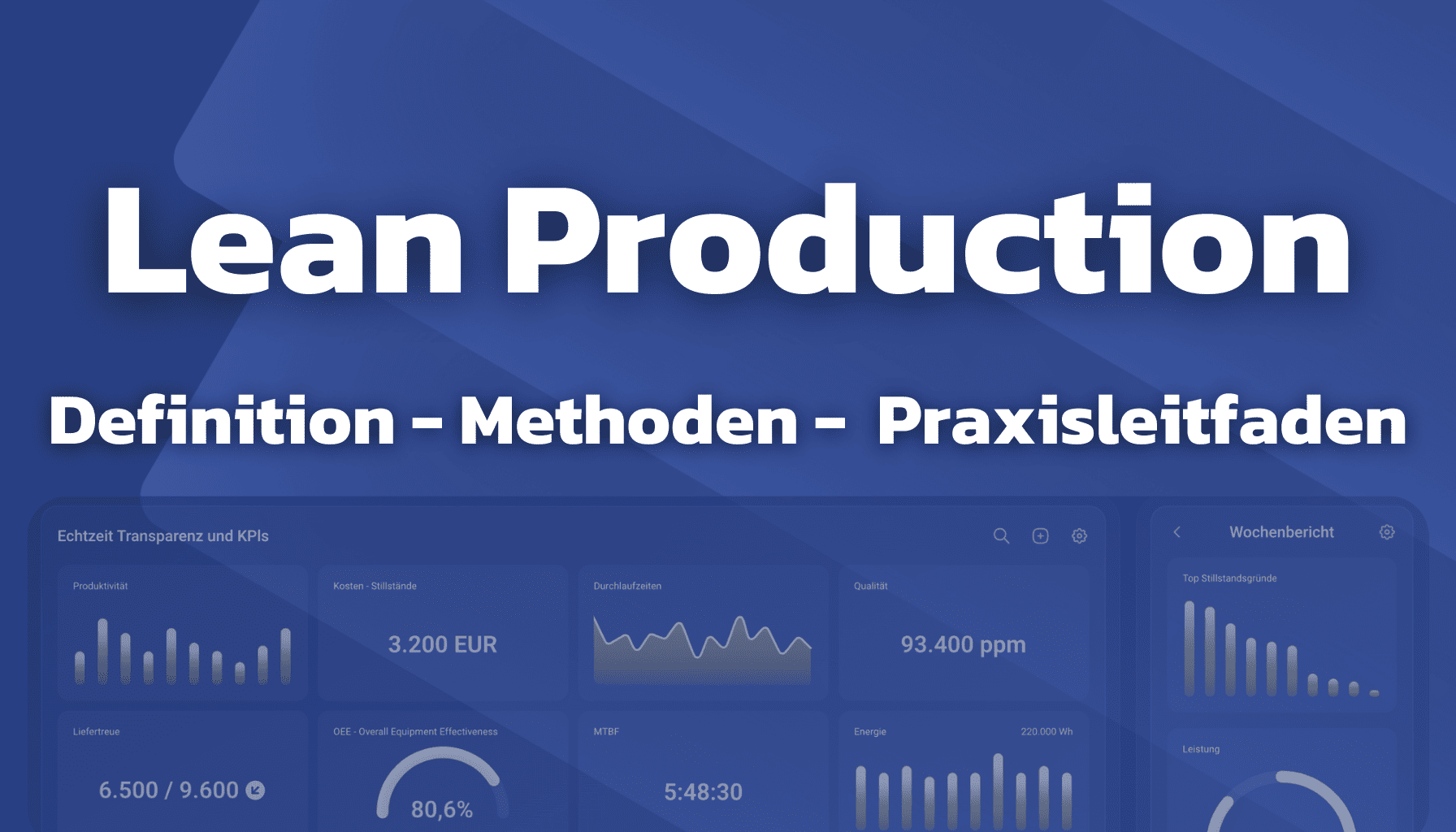
Inhaltsverzeichnis
Einführung in Lean Production
Was ist Lean Production? Eine klare Definition
Lean Production (schlanke Produktion) ist ein systematischer Ansatz zur Optimierung von Produktionsprozessen mit dem Ziel, Verschwendung zu minimieren und Wertschöpfung zu maximieren.
Kernelemente:
- Mehr erreichen mit weniger Ressourcen
- Fokus auf Wertschöpfung aus Kundensicht
- Unternehmensphilosophie und Methodensammlung
Lean Production Prinzipien
Weniger Ressourcen
Effizienter Einsatz von Material und Personal
Wertschöpfung
Fokus aus Kundensicht
Philosophie
Unternehmensphilosophie und Methoden
Warum ist Lean Production wichtig?
Heutige Herausforderungen für Unternehmen:
- Globalisierte Märkte und intensiver Wettbewerb
- Steigende Kundenerwartungen an Qualität und Individualität
- Kürzere Produktlebenszyklen
- Volatilere Nachfrage und Lieferketten
Lean Production bietet hier Lösungen durch:
- Verbesserte Reaktionsfähigkeit
- Geringere Kosten
- Kürzere Durchlaufzeiten
- Höhere Produktqualität
Bedeutung für Unternehmen
Typische Verbesserungen nach erfolgreicher Implementierung:
- 15-30% Produktivitätssteigerung
- 50-90% kürzere Durchlaufzeiten
- 25-75% Qualitätsverbesserung
- 60-90% Bestandsreduzierung
Geschichte und Ursprung
Von Toyota zum globalen Standard
- 1950er Jahre: Entwicklung des Toyota-Produktionssystems (TPS) durch Taiichi Ohno
- 1990: MIT-Studie "The Machine That Changed the World" prägt den Begriff "Lean Production"
- Heute: Globale Verbreitung in nahezu allen Branchen und Unternehmensgrößen
Entwicklung von Toyota zum globalen Standard
1950er
Toyota-Produktionssystem (TPS) durch Taiichi Ohno
1990
MIT-Studie prägt "Lean Production"
Heute
Globale Verbreitung in allen Branchen
Lean Production als Teil des Lean Managements
- Lean Production: Fokus auf Optimierung der Fertigung
- Lean Management: Erweiterung der Prinzipien auf alle Unternehmensbereiche
- Ganzheitlicher Ansatz: Für durchgängige Wertschöpfung
Zusammenfassung: Lean Production begann bei Toyota, wurde durch die MIT-Studie global bekannt und ist heute ein Standard, der sich im Lean Management auf alle Unternehmensbereiche erstreckt.
8 Gestaltungsprinzipien im Überblick
Die 8 Prinzipien der Lean Production
1.
Verschwendung vermeiden
Alles eliminieren, was keinen Wert schafft
2. Ressourceneffizienz
Optimale Nutzung von Material und Personal
3.
Kontinuierliche Verbesserung
Stetige inkrementelle Verbesserungen
4.
Standardisierung
Beste bekannte Methode definieren
5.
Null-Fehler-Prinzip
Fehlerprävention statt Kontrolle
6.
Fließprinzip
Unterbrechungsfreier Materialfluss
7.
Pull-Prinzip & Just-in-Time
Produktion nur bei Bedarf
8. Mitarbeiterorientierung
Visuelles Management und Einbindung
Die 7+1 Arten der Verschwendung
TIMWOOD + Ungenutztes Potenzial:
- Transport: Unnötige Bewegung von Material/Produkten
- Inventory: Überschüssige Bestände
- Motion: Überflüssige Bewegungen von Mitarbeitern
- Waiting: Wartezeiten und Leerlauf
- Overproduction: Herstellung ohne konkreten Bedarf
- Overprocessing: Unnötige Prozessschritte
- Defects: Qualitätsmängel und Ausschuss
- + Ungenutztes Mitarbeiterpotenzial: Nicht genutzte Fähigkeiten/Ideen
Die 7+1 Arten der Verschwendung
Transport
Unnötige Materialbewegung
Inventory
Überschüssige Bestände
Motion
Überflüssige Bewegungen
Waiting
Wartezeiten und Leerlauf
Overproduction
Herstellung ohne Bedarf
Overprocessing
Unnötige Prozessschritte
Defects
Qualitätsmängel und Ausschuss
+ Mitarbeiterpotenzial
Nicht genutzte Fähigkeiten/Ideen
Zusammenfassung: Die 8 Prinzipien und 7+1 Arten der Verschwendung bilden das Fundament der Lean Production, um Prozesse zu optimieren und Wertschöpfung zu maximieren.
Hauptziele der Lean Production
- Produktivitätssteigerung durch optimierten Ressourceneinsatz
- Qualitätsverbesserung mit weniger Fehlern und Ausschuss
- Flexibilitätssteigerung für schnelle Anpassung an Kundenwünsche
- Durchlaufzeitverkürzung vom Rohstoff bis zum fertigen Produkt
Vorteile für Unternehmen
Wirtschaftliche Vorteile:
- Geringere Kosten durch weniger Verschwendung
- Reduzierte Kapitalbindung durch niedrigere Bestände
- Höhere Kundenzufriedenheit durch bessere Qualität und Liefertreue
- Bessere Wettbewerbsposition durch Flexibilität und Reaktionsfähigkeit
Organisatorische Vorteile:
- Höhere Transparenz der Prozesse
- Verbesserte Problemlösungskompetenz
- Stärkere Mitarbeitermotivation und -einbindung
- Nachhaltigere Unternehmenskultur
Zusammenfassung: Lean Production zielt auf Produktivität, Qualität, Flexibilität und kürzere Durchlaufzeiten ab, mit wirtschaftlichen und organisatorischen Vorteilen für Unternehmen.
Potenzielle Risiken:
- Störanfälligkeit durch minimale Pufferbestände
- Erhöhte Transportfrequenz mit potenziellen Umweltauswirkungen
- Abhängigkeit von stabilen Lieferketten und zuverlässigen Zulieferern
Aktuelle Herausforderungen im Jahr 2025:
- Balance zwischen Effizienz und Resilienz
- Integration von Nachhaltigkeitsaspekten
- Kombination von Lean und Digitalisierung
Zusammenfassung: Lean Production birgt Risiken wie Störanfälligkeit und Abhängigkeit von Lieferketten, während 2025 Herausforderungen wie Nachhaltigkeit und Digitalisierung im Fokus stehen.
Schlüsselmethoden im Überblick
Methode | Beschreibung | Hauptnutzen |
---|---|---|
5S | Arbeitsplatzorganisation (Sortieren, Systematisieren, Säubern, Standardisieren, Selbstdisziplin) | Ordnung, Übersicht, Effizienz |
Kanban | Visuelles System zur Produktionssteuerung | Bestandsreduzierung, Pull-Produktion |
SMED | Single Minute Exchange of Die – Schnellrüsten | Flexibilität, kleinere Losgrößen |
TPM | Total Productive Maintenance | Maximale Anlageneffizienz |
Poka-Yoke | Fehlerverhinderungstechniken | Qualitätssicherung |
JIT | Just-in-Time Produktion | Minimale Bestände, kurze Durchlaufzeiten |
Kaizen | Kontinuierlicher Verbesserungsprozess | Stetige Evolution aller Prozesse |
Wertstromanalyse | Visualisierung und Analyse des Materialflusses | Identifikation von Verschwendung |
Die Lean Toolbox: Wichtigste Methoden
5S
Ordnung und Effizienz
Kanban
Pull-Produktion
SMED
Schnellrüsten
TPM
Anlageneffizienz
Poka-Yoke
Fehlerverhinderung
JIT
Just-in-Time
Kaizen
Kontinuierliche Verbesserung
Wertstromanalyse
Verschwendung identifizieren
Praxisbeispiele
Erfolgreiche Implementierungen:
- Automobilindustrie: Kanban-System reduziert Bestände um 35%, Flächenbedarf um 25%
- Elektronikfertigung: SMED-Implementierung senkt Rüstzeiten von 45 auf unter 10 Minuten
- Maschinenbau: 5S und Wertstromanalyse steigern Produktivität um 25%
Zusammenfassung: Lean-Methoden wie 5S, Kanban und Wertstromanalyse bieten praktische Werkzeuge zur Optimierung, mit messbaren Erfolgen in verschiedenen Branchen.
Lean-Methoden digital umsetzen
Mit Symestic Cloud MES digitalisieren Sie Lean-Methoden wie Kanban und Wertstromanalyse – steigern Sie Ihre Produktivität um bis zu 25% in 30 Tagen.
Testen Sie Symestic 30 Tage – inklusive Support für Ihren Erfolg.
Wie Cloud MES Lean-Prinzipien unterstützt
Integration von Lean und Digitalisierung:
- Echtzeit-Transparenz über alle Produktionsprozesse
- Automatische Datenerfassung statt manueller Aufschreibungen
- Datenbasierte Entscheidungen anstelle von Bauchgefühl
- Digitale Kanban-Boards und elektronische Pull-Systeme
- Automatische Erkennung von Verschwendung durch Analysetools
Integration von Lean Production und Cloud MES
Echtzeit-Transparenz
Alle Prozesse live einsehen
Automatische Datenerfassung
Keine manuellen Eingaben
Digitale Kanban-Boards
Effiziente Pull-Systeme
Vorteile von Cloud MES
- Skalierbarkeit: Mitwachsen mit den Unternehmensanforderungen
- Schnelle Implementierung: Keine umfangreiche IT-Infrastruktur nötig
- Standortübergreifende Standardisierung: Konsistente Prozesse an allen Standorten
- Mobilität: Zugriff von überall und jedem Gerät
- Automatische Updates: Immer aktuelle Funktionen ohne eigenen Wartungsaufwand
Praxisbeispiel: Cloud MES
- Automatische Datenerfassung reduziert manuelle Eingaben um 85%
- Echtzeit-KPIs ermöglichen sofortige Reaktion auf Abweichungen
- Digitales Shopfloor Management ersetzt Papier und Excel
- Integration von IoT-Geräten für umfassende Prozessüberwachung
Zusammenfassung: Cloud MES unterstützt Lean-Prinzipien durch Echtzeit-Daten, Automatisierung und digitale Tools, wie das Praxisbeispiel Symestic zeigt.
Erleben Sie Lean mit Symestic Cloud MES
Reduzieren Sie manuelle Eingaben um 85% und optimieren Sie Ihre Lean-Prozesse mit Symestic Cloud MES – testen Sie es 30 Tage kostenlos!
Testen Sie Symestic 30 Tage – inklusive Support für Ihren Erfolg.
Synergien zwischen Lean und Digitalisierung
Wie Industrie 4.0 Lean Production verstärkt:
- KI-gestützte Analyse von Produktionsdaten zur Verschwendungsidentifikation
- IoT-Sensoren für Echtzeit-Überwachung von Prozessen und Anlagen
- Digitale Zwillinge zur Simulation und Optimierung von Produktionsabläufen
- Augmented Reality zur Unterstützung der Mitarbeiter bei Montage und Wartung
Lean 4.0: Verschmelzung von Lean Production und Industrie 4.0
KI-Analyse
Verschwendung erkennen
IoT-Sensoren
Echtzeit-Überwachung
Digitale Zwillinge
Prozesse optimieren
Zukunftstrends 2025
- Predictive Maintenance: Vorausschauende Wartung basierend auf Echtzeitdaten
- Autonome Produktionssysteme: Selbstoptimierende Prozesse durch KI
- Digital Andon: Elektronische Eskalationssysteme in Echtzeit
- Smarte Kanban-Systeme: Automatische Nachbestellung durch IoT-Technologie
- Datengetriebenes Kaizen: Kontinuierliche Verbesserung auf Basis umfassender Datenanalyse
Zusammenfassung: Industrie 4.0 verstärkt Lean durch Technologien wie KI und IoT, mit Trends wie Predictive Maintenance und datengetriebenem Kaizen für 2025.
Schritt-für-Schritt-Ansatz
- Führungskräfte schulen und sensibilisieren
- Ist-Zustand analysieren (Wertstromanalyse)
- Pilotbereich auswählen und erste Methoden implementieren
- Mitarbeiter einbeziehen und qualifizieren
- Schritt für Schritt ausrollen und Standards etablieren
- Erfolge messen und kommunizieren
- Kontinuierlichen Verbesserungsprozess etablieren
Roadmap zur Lean Implementation
Schritt 1
Führungskräfte schulen
Schritt 2
Ist-Zustand analysieren
Schritt 3
Pilotbereich auswählen
Schritt 4-7
Ausrollen & Verbessern
Tipps für erfolgreiche Umsetzung
- Lean als Philosophie, nicht als Toolbox verstehen
- Führungsebene als Vorbild und Treiber einbinden
- Auf kulturellen Wandel fokussieren, nicht nur auf Methoden
- Klein anfangen, schnell Erfolge erzielen und kommunizieren
- Mitarbeiter nicht nur einbeziehen, sondern befähigen
- Lean-Reise als Marathon, nicht als Sprint verstehen
Zusammenfassung: Ein schrittweiser Ansatz mit Fokus auf Schulung, Pilotprojekten und kulturellem Wandel sorgt für eine erfolgreiche Lean-Umsetzung.
Zusammenfassung
Lean Production ist und bleibt ein Erfolgskonzept, weil es:
- Fundamentale Probleme der Verschwendung adressiert
- Auf bewährten Prinzipien basiert, die zeitlos sind
- Anpassungsfähig an unterschiedliche Branchen und Unternehmensgrößen ist
- Sich kontinuierlich weiterentwickelt und neue Technologien integriert
Ausblick 2025 und darüber hinaus
- Hybride Lean-Ansätze: Balance zwischen Effizienz und Resilienz
- Nachhaltige Lean Production: Integration von ökologischen Aspekten
- Lean Digital: Verschmelzung von Lean-Prinzipien und digitalen Technologien
- Human-Centered Lean: Stärkerer Fokus auf menschliche Aspekte im Zeitalter der Automatisierung
Testen Sie SYMESTIC Cloud MES kostenlos
Erleben Sie, wie SYMESTIC Cloud MES Ihre Lean-Initiative unterstützen kann:
- 30 Tage kostenlos testen ohne Verpflichtung
- Persönliche Beratung durch unsere Lean-Experten
- Individuelle Konfiguration passend zu Ihren Prozessen
- Schnelle Implementierung ohne großen IT-Aufwand
SYMESTIC Cloud MES: Lean Production digital umsetzen
30 Tage Test
Kostenlos und unverbindlich
Persönliche Beratung
Durch Lean-Experten
Schnelle Implementierung
Ohne großen IT-Aufwand
Abschluss: Lean Production bleibt ein zeitloses Erfolgskonzept, das sich mit digitalen Lösungen wie Symestic Cloud MES weiterentwickelt.
Starten Sie Ihre Lean-Reise mit Symestic
SYMESTIC Cloud MES unterstützt Ihre Lean-Initiative mit Echtzeit-Daten und Automatisierung – testen Sie es 30 Tage kostenlos!
Testen Sie Symestic 30 Tage – inklusive Support für Ihren Erfolg.
Exklusives Whitepaper
Lernen Sie die modernsten Ansätze der Industrie 4.0, die Sie in Ihrer Produktion schon morgen umsetzen können, um innerhalb von 4 Wochen Ihre Kosten um gut 20% zu reduzieren.
mehr erfahren