What is an MES (Manufacturing Execution System)?
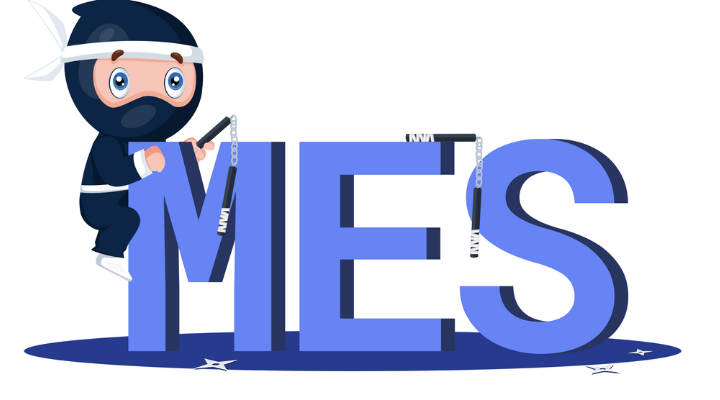
This article answers the following questions on manufacturing execution systems (MES):
- What is an MES?
- What are the main benefits of an MES?
- What are the core functions of an MES?
- Which interfaces and levels are there?
- What are the latest technologies and trends?
- What is the easiest, least disruptive way to introduce an MES?
Our goal is to provide you with the knowledge you need to benefit from MES at your company.
So let’s get started!
What is an MES?
A manufacturing execution system (MES) is a computerized system comprising a set of dynamic, software-based services for monitoring, tracking, documenting, and to some extent also controlling the product production process from start to finish.
The MES - constituting a functional layer between the machines (the OT layer) and administration or an enterprise resource planning (ERP) system (the IT layer) - provides the management data that are needed to quickly make decisions, ensure transparency in real time, and optimize processes.
An MES executes production processes on the basis of information, thus increasing a company’s overall productivity and therefore also its profitability. In fact, considering today’s high demands on performance and rapidly changing production environments, it’s now essential to have one in place. A report by Data Bridge Market Research predicts that the global MES market will reach a volume of 39.67 billion USD as early as the year 2029. The principal factors driving this growth are cost pressures in the highly competitive manufacturing sector. The demand is being met both by older on-premises MES systems and, to a rapidly growing extent, by cloud-based software as a service (SaaS) systems with low provisioning and project costs.
Many people use the term “production data collection” or “machine data collection” instead of MES. They are not the same thing, however. For detailed explanations of these terms, please see our article on production data collection.
What are the main benefits of MES?
More efficient production
An MES helps boost the efficiency of production and overall equipment effectiveness (OEE) by providing transparency and real-time analyses. Large data volumes are crunched to analyze the factors of performance, availability, and quality.
Better quality
Quality is improved by leveraging real-time quality data and digitally captured causes of problems. What’s more, MES can immediately spot and prevent downstream or large-scale faults. This reduces rejects and slashes resource consumption.
Reduced stocks
The MES can automatically report information on the numbers of units produced, rejects, and quality to the enterprise resource planning (ERP) system, thus enabling it to reduce the quantities of materials kept in stock. Administrative departments, like those responsible for logistics or purchasing, are then consistently aware of how production is progressing and the amounts of materials that are additionally required. These interfaces and the resulting greater transparency permit better management of the “work in process” (WIP), thus generating savings in the areas of production, transportation, and storage. Monitoring of stocks, which in some cases is still done by hand, can then be almost completely eliminated.
Paperless manufacturing
Digital operator guidance can send production orders, along with the corresponding processes and activities across all work steps. To some extent they can even be linked to production aids. This immediately eliminates the need to print out all order documents.
Traceability and product lifecycle document
Using the time, order, product data, or serial number in an MES, it’s possible to generate a digital product lifecycle document containing all relevant information such as machining times, process values, machine states, or quality data and subsequently use it for traceability analysis if and as required. If production resources are integrated, process control parameters can be taken from the MES that, for example, don’t allow a subsequent step to be performed until the current one has been completed, verified by an OK signal, and registered in the MES. These functions together form a zero-defect process control system with process interlocking.
What are the core functions of an MES?
VDI guideline 5600 describes the seven core functions of an MES that are the basis for operating nearly any kind of system and should be included every modern production system. This is true despite the fact that, thanks to SaaS, a monolithic system is no longer a prerequisite.
Production planning
Completion of the work list while taking the prevailing restrictions on production into account.
Management of operational resources
Deadline and provision of technically functional resources as required.
Management of materials
On-time supply and disposal of materials to meet production requirements and manage work in progress (materials not included in the vendor-managed inventory).
Personnel management
Timely provision of appropriately qualified personnel for the production process, while taking personnel-related capacity data (e.g. weekly working hours / shift schedules) into account.
Data capture
Event-controlled capture of data from the process. Besides automatic data transfer, semiautomatic (e.g. by a scanner) and manual data capture are possible.
Quality management
This comprises activities that concern the immediate production process and serve to ensure product and process quality.
Information management
This is a switching point for integrating other MES tasks and performing all workflows while working through the order backlog and optimizing processes.
What interfaces and levels are there?
In the context of MES, ISA 95 defines the interfaces between OT and IT. The various levels between the technology and the business process are also considered.
Level 4 – ERP: business planning and logistics
Level 3 – MES: management of manufacturing operations
Level 2 – process control systems: batch control
Level 1 – process control systems: continuous control
Level 0 – process control systems: discrete control
The main interface to third-party systems is that between the MES and the ERP system. Here master and movement data on products, work plans, bills of material, and orders are passed by the ERP to the MES. In the opposite direction, the MES typically provides feedback on orders and movement data on the individual objects.
Advanced technologies and trends
Modern MES systems are modular and based on advanced cloud technologies. The MES is service-oriented and networked with other services and systems. Topics such as analytics, data streaming, and artificial intelligence combine with the data and services of a modern MES to form the backbone of a modern “smart factory”.
What is the easiest, least disruptive way to introduce an MES?
Take a look at the sections on production metrics and production control or have one of our experts show you, in an individual Web session, just how quickly and easily this can now be accomplished.