OEE calculation: formula in detail, common mistakes & best practices
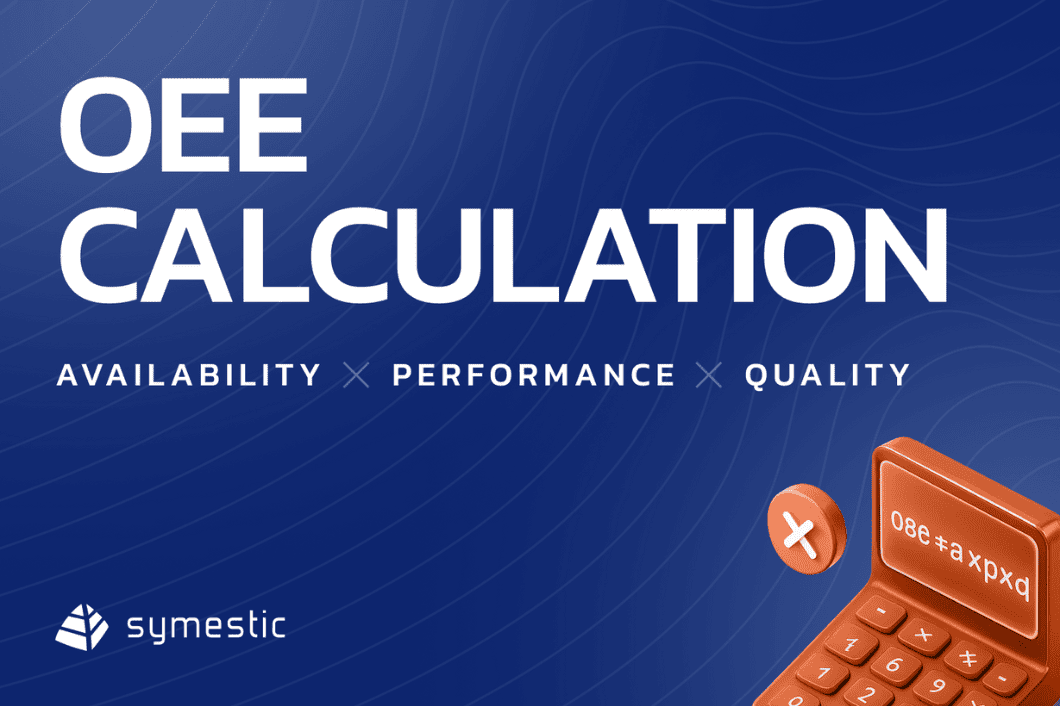
Your OEE Knowledge Journey
Our three-part guide comprehensively explores Overall Equipment Effectiveness—from fundamentals and calculations to digital implementation.
1. OEE Basics
Definition, factors, and benefits of Overall Equipment Effectiveness for your production.
Read More2. OEE Calculation
Detailed formula, common mistakes, and best practices for precise OEE calculations.
Current ArticleTable of Contents
- Organizational Preparation for OEE Calculation
- The OEE Formula in Detail
- Calculating Availability
- Calculating Performance
- Calculating Quality
- Overall OEE Calculation
- Common Calculation Errors and How to Avoid Them
- Industry-Specific Calculation Variants
- OEE Calculation for Continuous Processes
- Loss Analysis for OEE Optimization
- OEE Calculation in Industry 4.0
- OEE Best Practices
- OEE Calculation Tools and Software
Introduction: Precise OEE Calculation as the Basis for Production Optimization
The precise calculation of the OEE metric (Overall Equipment Effectiveness) is the key to systematic production optimization. Unlike superficial production metrics, the OEE calculation provides a precise, mathematically grounded insight into your manufacturing efficiency.
A correctly performed OEE calculation:
- Quantifies production losses in dollars rather than abstract percentages
- Identifies gradual performance declines before they lead to failures
- Enables data-driven setup optimization through variant analysis
- Provides verifiable ROI calculations for process optimizations
This technical guide walks you through each component of the OEE calculation with precise formulas, practical examples, and industry-specific calculation variants.
You’ll gain the necessary mathematical and methodological tools to use OEE as a strategic instrument for productivity enhancement.
Organizational Preparation for OEE Calculation
Before you can calculate OEE, certain organizational prerequisites must be established:
1. Define Data Collection Strategy
Decide between manual and automated data collection:
Collection Method | Advantages | Disadvantages | Typical Application |
---|---|---|---|
Manual (Paper Forms) | Low initial costs | Error-prone, time-delayed | Small businesses, pilot projects |
Semi-Automated (Tablets) | Faster data collection | Requires digital infrastructure | Mid-sized production |
Fully Automated (IoT Sensors) | Real-time data, captures micro-downtimes | Higher investment costs | Large-scale production, Industry 4.0 |
2. Select Pilot Equipment
For your initial OEE calculation, ideally choose:
- A bottleneck in the production process
- A representative machine with typical loss sources
- Equipment with economic significance for your operation
3. Determine Calculation Period
The choice of calculation period directly affects the meaningfulness of your OEE results:
Calculation Period | Typical Application | Considerations |
---|---|---|
Shift | Daily shop floor management | High data granularity, shows operator influences |
Day | Production management, daily control | Good balance between detail and overview |
Week | Medium-term optimization | Smooths daily fluctuations |
Month | Management reporting | Trends visible, details may be lost |
4. Assemble OEE Team
An effective OEE calculation team ideally includes:
Capture and Visualize OEE in Real Time
From data chaos to clear dashboards: How to achieve professional OEE data capture
From Theory to Practice:
- Automated data capture directly at the machine
- Real-time calculation of all OEE factors
- Customizable dashboards for different user groups
- Trend analyses for better optimization decisions
The OEE Formula in Detail: Technical Foundation
The OEE calculation is based on the multiplicative combination of three core factors:
This mathematical structure has critical implications:
-
Multiplicative Relationship: The multiplication amplifies deficits in individual factors, making OEE highly sensitive to weaknesses.
-
Mathematical Properties:
- The OEE value always lies between 0 and 1 (or 0% and 100%)
- The OEE value cannot exceed the lowest individual factor
- An OEE value above 100% is mathematically impossible and indicates calculation errors
- The Detailed Formulas:
OEE = Availability × Performance × Quality
Availability = Actual Operating Time / Planned Production Time
Performance = (Ideal Cycle Time × Number of Parts Produced) / Actual Operating Time
Quality = Good Parts / Number of Parts Produced
Example Calculation with Numbers
A manufacturing company recorded the following values:
- Planned Production Time: 480 minutes (8 hours)
- Downtime: 60 minutes
- Ideal Cycle Time: 2 minutes per part
- Parts Produced: 180 units
- Defect-Free Parts: 171 units
The OEE calculation proceeds in three steps:
Practical Example: OEE Calculation
Step 1: Calculate Availability
Availability = (480 - 60) / 480 = 420 / 480 = 0.875 = 87.5%
Step 2: Calculate Performance
Ideal Output = 420 / 2 = 210 parts Performance = 180 / 210 = 0.857 = 85.7%
Step 3: Calculate Quality
Quality = 171 / 180 = 0.95 = 95%
Overall OEE Calculation
OEE = 0.875 × 0.857 × 0.95 = 0.712 = 71.2%
This value of 71.2% indicates that the equipment achieves just over 70% of its theoretical capacity.
Calculating Availability: Technical Detailed Guide
The availability factor is mathematically defined as:
Availability = Actual Operating Time / Planned Production Time
Precise Definition of Time Components
For an accurate calculation, time components must be precisely defined:
- Calendar Time: Total available time (24 hours × 7 days)
- Operating Time: Time the equipment is staffed (e.g., 3-shift operation)
- Planned Production Time: Operating time minus planned downtimes
- Actual Operating Time: Planned production time minus unplanned downtimes
Downtime Categorization for Availability Calculation
Precise categorization of downtimes is critical:
Downtime Type | Impact on Availability | Examples | Collection Method |
---|---|---|---|
Planned Downtimes | Not included in calculation | Maintenance, shift changes, breaks | Work schedule, shift plan |
Unplanned Downtimes >5 Min | Reduce availability | Machine failures, material shortages | Fault reports, downtime logs |
Micro-Downtimes <5 Min | Depends on definition | Material jams, minor adjustments | Automated IoT capture |
Setup Times | Depends on definition | Tool changes, retooling | Setup logs, MES system |
Practical Example: Availability Calculation in Metal Processing
Shift Length: 480 minutes (8 hours)
Planned Breaks: 30 minutes
Planned Maintenance: 20 minutes
Planned Production Time: 480 - 30 - 20 = 430 minutes
Unplanned Downtimes:
- Machine Failure: 35 minutes
- Material Shortage: 18 minutes
- Tool Breakage: 12 minutes
Total Unplanned Downtime: 65 minutes
Actual Operating Time: 430 - 65 = 365 minutes
Availability = 365 / 430 = 0.849 = 84.9%
Common Sources of Error in Availability Calculation
-
Non-Capture of Micro-Downtimes: In a shift, fifty 3-minute stops can result in a total loss of 150 minutes, often undetected in manual collection.
-
Incorrect Assignment of Planned Downtimes: Maintenance times are sometimes mistakenly categorized as unplanned downtimes, artificially reducing availability.
-
Inconsistent Definitions of Setup Times: Depending on the company, setup times are treated differently. A consistent definition is crucial.
Technical Optimization of Availability Capture
-
IoT Sensors for Real-Time Capture: Automated capture of machine signals enables identification of micro-downtimes from 3 seconds.
-
Downtime Coding: Implement a standardized coding system for downtime causes (e.g., technical, organizational, material, or personnel-related).
-
OEE Dashboards: Visualize downtime in real time to enable immediate responses.
Calculating Performance: Precise Determination of the Speed Factor
The performance factor measures how closely the actual production speed aligns with the theoretically possible speed:
Performance = (Ideal Cycle Time × Number of Parts Produced) / Actual Operating Time
Alternatively, the formula can be expressed as:
Performance = Actual Production Rate / Ideal Production Rate
Determining the Ideal Cycle Time
Accurately determining the ideal cycle time is critical for a realistic performance calculation:
Method | Description | Advantages and Disadvantages |
---|---|---|
Manufacturer Specifications | Technical data from the machine manufacturer | Often overly optimistic, does not account for operating conditions |
Design Capacity | Designed throughput of the equipment | Closer to reality, but excludes operational influences |
Best Demonstrated Performance | Best performance under real conditions | Realistic, but may not be consistently achievable |
Statistical Analysis | Capture of the fastest 10% of cycles | Scientific approach, practical |
Recommended Approach: Combine Best Demonstrated Performance with statistical analysis and verify results through time studies.
Performance Calculation with Time Units
Performance can be calculated using different time units:
Example with Hours
Actual Operating Time: 6.5 hours (390 minutes)
Ideal Cycle Time: 30 seconds per part = 0.5 minutes = 0.00833 hours
Parts Produced: 650 units
Performance = (0.00833 × 650) / 6.5 = 5.41 / 6.5 = 0.832 = 83.2%
Example with Seconds (Highly Precise)
Actual Operating Time: 390 minutes = 23,400 seconds
Ideal Cycle Time: 30 seconds per part
Parts Produced: 650 units
Performance = (30 × 650) / 23,400 = 19,500 / 23,400 = 0.833 = 83.3%
The minimal deviation (83.2% vs. 83.3%) highlights the importance of consistently using the same time units.
Specifics of Performance Calculation
-
Product Mix Influence: For different products with varying cycle times, a weighted calculation is required:
Example
Product A: 400 parts, ideal cycle time 30 seconds
Product B: 250 parts, ideal cycle time 45 seconds
Total Ideal Production Time = (400 × 30) + (250 × 45) = 12,000 + 11,250 = 23,250 seconds
Performance = 23,250 / Actual Operating Time in seconds -
Performance Values Above 100%: A performance value exceeding 100% clearly indicates an ideal cycle time set too low. In such cases, the reference time should be reviewed and adjusted.
-
Dynamic Speed Adjustment: For equipment with variable speeds (e.g., depending on materials or temperature), the ideal cycle time may fluctuate. A dynamic calculation based on current conditions is necessary.
Practical Example: Performance Calculation in the Packaging Industry
Actual Operating Time: 405 minutes = 24,300 seconds Ideal Cycle Time: 4 seconds per package Packages Produced: 5,000 units Ideal Output in 24,300 seconds = 24,300 / 4 = 6,075 packages Performance = 5,000 / 6,075 = 0.823 = 82.3%
Alternatively with Direct Formula:
Performance = (4 × 5,000) / 24,300 = 20,000 / 24,300 = 0.823 = 82.3%
Technical Optimization of Performance Capture
-
Automated Cycle Time Capture: Implement sensors that measure cycle times in real time and detect variations.
-
Statistical Process Limits: Define upper and lower control limits for cycle times to identify abnormal speed fluctuations.
-
Performance Trend Analysis: Monitor performance trends over time to detect gradual deteriorations early.
Calculating Quality: Precise Capture of Defect-Free Production
The quality factor quantifies the proportion of defect-free production relative to total production:
Quality = Number of Good Parts / Total Number of Parts Produced
The quality component of OEE differs from traditional quality metrics by focusing on scrap and rework directly at the point of origin.
Precise Definition of "Good Parts"
For an accurate quality calculation, the definition of "good parts" is critical:
Category | For OEE Calculation | Reason |
---|---|---|
Defect-Free Parts | Count as "good" | Meet quality requirements without rework |
Parts with Rework | Do NOT count as "good" | Require additional resource expenditure |
Scrap | Do NOT count as "good" | Complete loss of value creation |
Tooling Parts/Samples | Depends on definition | Requires clear regulation |
Calculation with Different Quality Losses
A differentiated quality calculation distinguishes between various types of quality losses:
Example
Total Production: 1,000 parts
Defect-Free Parts: 940 parts
Rework: 35 parts
Scrap: 25 parts
Quality = 940 / 1,000 = 0.94 = 94%
Alternatively, the calculation can be performed via losses:
Quality = (1,000 - 35 - 25) / 1,000 = 940 / 1,000 = 0.94 = 94%
Timing of Quality Control
The timing of quality control significantly impacts the OEE calculation:
Control Timing | Impact on OEE Calculation | Considerations |
---|---|---|
Immediately After Production | Timely data, immediate feedback | Not all defects are immediately detectable |
After Intermediate Storage | More comprehensive quality assessment | Time delay in calculation |
After Further Process Steps | Later defect detection | Complex cause attribution |
Best Practice: Implement a multi-stage quality system that includes both immediate and downstream controls, clearly defining which data feeds into the OEE calculation.
Quality Calculation for Continuous Processes
In continuous processes (e.g., chemical, paper production), quality is calculated differently:
Example
Quality = Quantity Within Specification / Total Quantity Produced
Example:
Total Production: 10,000 liters
Specification-Compliant Production: 9,700 liters
Quality = 9,700 / 10,000 = 0.97 = 97%
Practical Example: Quality Calculation in Electronics Manufacturing
Total Production: 5,000 circuit boards
Defect-Free Circuit Boards: 4,800
Circuit Boards with Soldering Errors (Scrap): 150
Circuit Boards with Repairable Defects (Rework): 50
Quality = 4,800 / 5,000 = 0.96 = 96%
Common Sources of Error in Quality Calculation
-
Including Rework as "Good Parts": Rework incurs additional costs and should be considered a quality loss.
-
Lack of Traceability for Quality Issues: Without clear cause attribution, targeted improvements are impossible.
-
Time Delays in Quality Capture: Quality data must be promptly integrated into the OEE calculation to deliver meaningful results.
Overall OEE Calculation and Interpretation of Results
The Overall Equipment Effectiveness (OEE) is calculated by multiplying the three core factors:
OEE = Availability × Performance × Quality
OEE Calculation in Detail
Using the values from our previous examples:
- Availability: 84.9%
- Performance: 82.3%
- Quality: 96%
OEE = 0.849 × 0.823 × 0.96 = 0.671 = 67.1%
Calculation Breakdown
Availability = 84.9% = 0.849 Performance = 82.3% = 0.823 Quality = 96.0% = 0.960 OEE = 0.849 × 0.823 × 0.960 = 0.671 = 67.1%
This OEE value of 67.1% indicates that the equipment is operating at approximately two-thirds of its maximum potential, highlighting opportunities for optimization.
Interpretation of OEE Values
OEE values provide a clear benchmark for assessing manufacturing efficiency:
OEE Value | Assessment | Typical Causes | Action Recommendation |
---|---|---|---|
<60% | Below Average | Significant losses in multiple factors | Comprehensive analysis of all factors, prioritize largest loss factor |
60-75% | Average | Typical for many companies without systematic OEE optimization | Targeted improvement of the weakest factor |
75-85% | Good | Established improvement processes | Fine-tuning and standardized processes |
>85% | World-Class | Highly developed processes with continuous optimization | Stabilization and process standardization |
Industry-Specific Benchmarks
The following table presents typical OEE benchmark values across various industries to contextualize your manufacturing efficiency:
Industry | Below Average | Average | Good | World-Class |
---|---|---|---|---|
Automotive Industry | < 70% | 70-85% | 85-90% | > 90% |
Process Industry (Continuous) | < 75% | 75-85% | 85-90% | > 90% |
Mechanical Engineering | < 60% | 60-75% | 75-85% | > 85% |
Plastics | < 65% | 65-80% | 80-85% | > 85% |
Food | < 60% | 60-75% | 75-80% | > 80% |
Pharmaceutical Industry | < 60% | 60-70% | 70-80% | > 80% |
Metal Processing | < 55% | 55-70% | 70-80% | > 80% |
Printing Industry | < 50% | 50-65% | 65-75% | > 75% |
Prioritizing Improvement Measures
A critical aspect of OEE calculation is prioritizing improvement measures based on the results:
-
Pareto Analysis of Losses: Identify the primary loss sources using the 80/20 principle.
-
Comparison of Factors: In our example, Performance at 82.3% is the weakest factor, so it should be optimized first.
-
ROI Analysis: Calculate the financial impact of improvements:
Example: Financial Impact
For equipment with 2,000 operating hours/year and a machine hourly rate of $250:
- Current OEE: 67.1%
- Target OEE after Improvement: 75%
- Difference: 7.9%
Additional Productive Time: 2,000 × 0.079 = 158 hours/year
Financial Benefit: 158 × $250 = $39,500/year
Common Calculation Errors and How to Avoid Them
Several specific errors frequently occur during OEE calculations, leading to inaccurate or misleading results:
1. Unrealistic Assumption of Ideal Cycle Time
Problem: The ideal cycle time is often taken from manufacturer specifications determined under lab conditions, leading to performance values exceeding 100%, which is mathematically impossible.
Example
Per Manufacturer: 3 seconds per part
Realistic Cycle Time: 4 seconds per part
Using Manufacturer Specification:
Performance = (3 × 1,000) / 3,300 = 0.909 = 90.9%
With 3.5-Second Cycles in Reality:
Actual Performance = (4 × 1,000) / 3,300 = 1.212 = 121.2% (impossible!)
Solution:
- Determine the ideal cycle time through tests under real production conditions.
- Use statistical methods: average of the top 10% of measured cycle times.
- Apply Best Demonstrated Performance under normal operating conditions.
2. Incomplete Capture of Downtimes
Problem: Micro-downtimes (under 5 minutes) are often overlooked in manual data collection, yet they can accumulate into significant losses.
Example
50 Micro-Downtimes of 3 Minutes Each = 150 minutes total loss (2.5 hours!)
With a planned production time of 8 hours, this represents a 31.25% availability loss.
Solution:
- Implement automated data collection that registers even short downtimes.
- Train employees to accurately record brief interruptions.
- Use IoT sensors to automatically capture downtimes starting from 3 seconds.
3. Incorrect Handling of Setup Times
Problem: Setup times are treated differently across companies in OEE calculations.
Example
Variant 1: Setup is planned non-production time → not included in OEE
Variant 2: Setup is unplanned downtime → reduces availability
Variant 3: Only setup times exceeding standard setup time reduce availability
Solution:
- Clearly define how setup times are handled in your OEE calculation.
- Consistently apply the same definition across the company.
- Document the approach to ensure comparability.
4. Incorrect Inclusion of Rework in Quality Calculation
Problem: Reworked parts are mistakenly counted as "good parts," distorting the quality component.
Example
1,000 parts produced
900 immediately defect-free parts
80 parts with rework
20 parts scrap
Incorrect Calculation: Quality = (900 + 80) / 1,000 = 0.98 = 98%
Correct Calculation: Quality = 900 / 1,000 = 0.9 = 90%
Solution:
- Count only parts that are defect-free on the first pass as "good."
- Record rework separately as a quality loss.
- Implement First Pass Yield (FPY) as a complementary metric.
5. Inconsistent Time Basis in Calculations
Problem: Using different time units (hours, minutes, seconds) can lead to calculation errors.
Example
Operating Time: 390 minutes
Cycle Time: 45 seconds
Incorrect Calculation with Mixed Units:
Performance = (45 × 500) / 390 = 57.7 (nonsense!)
Correct Calculation with Consistent Time Units:
Performance = (45 × 500) / (390 × 60) = 0.962 = 96.2%
Solution:
Industry-Specific Calculation Variants
OEE calculations must be tailored to the specific requirements of different industries to deliver meaningful results.
Automotive Industry
In automotive manufacturing, with its complex lines and takt-time-driven processes, the following adjustments are common:
Adjusted Performance Calculation for Linked Lines
Performance = Total Output / (Bottleneck Station Capacity × Operating Time)
Special Considerations:
- Quality calculation accounts for different defect classes with weighting.
- Availability often focuses on the bottleneck station.
- Just-In-Time (JIT) production requires consideration of material availability.
Process Industry (Chemical, Paper, Steel)
In continuous processes without discrete parts:
Adjusted Performance Calculation
Performance = Actual Throughput / Maximum Nominal Throughput
Special Considerations:
- Quality is defined by specification limits (within vs. outside specification).
- Availability accounts for partial load operations.
- Grade changes (product switches) are evaluated differently from complete downtimes.
Food and Beverage Industry
In the food industry with high hygiene standards:
Adjusted Availability Calculation
Availability = Operating Time / (Shift Time - Cleaning Time)
Special Considerations:
- Regular cleaning cycles (e.g., Clean-in-Place, CIP) are defined as planned non-production time.
- Quality includes not only product defects but also microbiological parameters.
- Shelf-life data influences the definition of "good products."
Pharmaceutical Industry
In the highly regulated pharmaceutical industry:
Adjusted Quality Calculation
Quality = (Produced Quantity - Scrap - Deviations - Quarantine) / Produced Quantity
Special Considerations:
OEE Calculation for Continuous Processes
Continuous manufacturing processes (e.g., in the chemical, paper, or steel industries) require an adapted OEE calculation since they do not produce discrete units.
Adapted Formulas for Continuous Processes
Availability: The calculation remains fundamentally the same but also considers partial load operation:
Availability = Productive Time / Planned Production Time
Performance: Instead of part counts, throughput is used:
Performance = Actual Throughput / Maximum Throughput
Quality: Relates to the quantity of product within specification limits:
Quality = Quantity Within Specification / Total Quantity Produced
Practical Calculation Example: Paper Manufacturing
Example
Planned Production Time: 24 hours
Downtimes: 2.5 hours
Partial Load Operation (75%): 4 hours
Maximum Throughput: 25 tons/hour
Average Throughput During Full Operation: 22 tons/hour
Average Throughput During Partial Load: 18 tons/hour
Total Production: 22 × 17.5 + 18 × 4 = 385 + 72 = 457 tons
Theoretical Maximum Production: 25 × 21.5 = 537.5 tons
Out of Specification: 23 tons
Availability = 21.5 / 24 = 0.896 = 89.6%
Performance = 457 / 537.5 = 0.85 = 85%
Quality = (457 - 23) / 457 = 0.95 = 95%
OEE = 0.896 × 0.85 × 0.95 = 0.724 = 72.4%
Special Considerations for Continuous Processes
-
Partial Load Operation: When operating at reduced speed, it is either:
- Calculated as a performance loss (Availability = 100%, Performance reduced)
- Or as an availability loss (Availability reduced, Performance = 100%) -
Product Switches (Grade-Change): Transition phases between product variants are, depending on definition:
- Treated as planned downtime (not included in OEE)
- Considered a performance loss (reduced speed during transition)
- Viewed as a quality loss (transitional product out of specification) -
Measurement Frequency: Continuous processes require continuous or high-frequency measurements:
- Flow meters for volume/weight
- Inline quality sensors for real-time data
- Process control systems (DCS) as data sources
The Six Big Losses: Loss Analysis for OEE Optimization
The "Six Big Losses" represent the six primary sources of inefficiency that negatively impact Overall Equipment Effectiveness (OEE). This systematic categorization enables targeted identification and quantification of improvement opportunities in manufacturing processes.
Overview: The Six Big Losses and Their Assignment
Loss Source | OEE Factor | Typical Causes | Typical Improvement Potential |
---|---|---|---|
1. Equipment Failures | Availability | Technical defects, tool breakage | 5-20% improvement |
2. Setup and Adjustment Times | Availability | Product changes, tool changes | 10-30% improvement |
3. Short Stops | Performance | Material jams, minor disruptions | 5-15% improvement |
4. Reduced Speed | Performance | Suboptimal settings, equipment wear | 5-25% improvement |
5. Startup Losses | Quality | Unstable processes after restart | 1-5% improvement |
6. Quality Losses | Quality | Process variations, material defects | 2-10% improvement |
Detailed Calculation Methods for the Six Big Losses
1. Equipment Failures
Equipment Failure Loss (%) = (Downtime / Planned Production Time) × 100
Example:
Downtime: 85 minutes
Planned Production Time: 480 minutes
Loss = (85 / 480) × 100 = 17.7%
2. Setup and Adjustment Times
Setup Time Loss (%) = (Setup Time / Planned Production Time) × 100
Example:
Setup Time: 45 minutes
Planned Production Time: 480 minutes
Loss = (45 / 480) × 100 = 9.4%
3. Short Stops
Short Stop Loss (%) = (Number of Parts at Ideal Speed Without Short Stops - Actual Parts Produced) / Number of Parts at Ideal Speed
Example:
Ideal Production Without Short Stops: 5,000 parts
Actual Production: 4,600 parts
Loss = (5,000 - 4,600) / 5,000 = 0.08 = 8%
4. Reduced Speed
Speed Loss (%) = (Ideal Cycle Time × Parts Produced) / Net Operating Time - 1
Example:
Ideal Cycle Time: 30 seconds
Parts Produced: 800
Net Operating Time: 450 minutes = 27,000 seconds
Loss = (30 × 800) / 27,000 - 1 = 24,000 / 27,000 - 1 = 0.889 - 1 = -0.111 = 11.1%
5. Startup Losses
Startup Loss (%) = Number of Scrap Parts During Startup / Total Parts Produced During Operating Time
Example:
Scrap During Startup: 25 parts
Total Production: 1,200 parts
Loss = 25 / 1,200 = 0.021 = 2.1%
6. Quality Losses During Stable Production
Quality Loss (%) = (Scrap + Rework During Stable Production) / Total Parts Produced
Example:
Scrap During Stable Production: 20 parts
Rework: 35 parts
Total Production: 1,200 parts
Loss = (20 + 35) / 1,200 = 55 / 1,200 = 0.046 = 4.6%
Loss Diagnosis with Pareto Analysis
Pareto Analysis helps identify the most significant loss sources and prioritize optimization efforts:
- Collect all loss data over a representative period.
- Sort losses by magnitude (descending order).
- Calculate cumulative percentages.
- Focus on the few loss types that account for 80% of total losses.
Example: Loss Analysis for a Packaging Line
Loss Analysis of a Packaging Line:
- Short Stops: 12% (material jams)
- Equipment Failures: 8% (conveyor belt defects)
- Setup Times: 7% (format changes)
- Reduced Speed: 6% (worn bearings)
- Quality Losses: 3% (misaligned gluing)
- Startup Losses: 1% (unstable parameters)
Top-2 Losses (Short Stops and Equipment Failures) account for 20% of 37% total loss = 54% of losses
OEE Calculation in the Context of Industry 4.0
Digital transformation and Industry 4.0 technologies revolutionize OEE calculation through real-time data, automated analytics, and predictive capabilities, enhancing manufacturing efficiency.
IoT-Based OEE Data Capture
Modern IoT sensors deliver highly precise real-time data for accurate OEE calculations:
Data Type | Capture Method | Advantages | Impact on OEE Calculation |
---|---|---|---|
Machine States | PLC Connection, I/O Signals | Automated capture without user intervention | Precise availability calculation, including micro-downtimes |
Cycle Time Capture | Photoelectric Sensors, Proximity Sensors | High accuracy, near-real-time data collection | Accurate real-time performance calculation |
Part Count Capture | Vision Systems, RFID Tracking | Automatic counting and identification | Precise input/output measurement for quality calculation |
Process Parameters | Temperature, Pressure, Vibration Sensors | Continuous monitoring of critical parameters | Early warning system for quality and performance issues |
Technical Setup:
Machine Signal → Edge Device → OEE Software → Dashboards
Key Interfaces:
- OPC UA for standardized machine communication
- MQTT for lightweight IoT communication
- REST APIs for integration with higher-level systems
Machine Learning for More Precise OEE Calculations
AI algorithms enhance OEE calculations through intelligent pattern recognition:
-
Automatic Downtime Categorization: Machine learning algorithms classify downtimes automatically based on patterns and signals, reducing manual inputs.
-
Dynamic Adjustment of Ideal Cycle Times: Self-learning systems adjust ideal cycle times based on product variants, materials, and environmental conditions.
-
More Precise Quality Prediction: Predictive quality uses process parameters to forecast quality issues before they occur.
Example
Traditional Calculation:
Fixed Ideal Cycle Time for Product A: 45 seconds
ML-Optimized Calculation:
Dynamic Ideal Cycle Time for Product A with Material X at Temperature Y: 42.3 seconds
Cloud-Based OEE Calculation for Global Production Networks
Cloud platforms enable cross-site OEE analysis:
Architecture:
Local Data Collection → Edge Computing (Preprocessing) → Cloud Platform → Global Dashboards
Advantages:
- Global standardization of OEE calculation
- Cross-site benchmarking
- Centralized data storage with decentralized access
- Scalable computing capacity for complex analyses
Digital Twin for OEE Simulation
Digital twins enable simulation of production processes for OEE forecasting and optimization:
-
What-If Analyses:
"How does OEE change if we reduce setup times by 20%?"
"What is the effect of a 5% increase in machine speed on quality?" -
Optimal Production Planning:
Simulation of different production sequences to minimize setup times
Calculation of optimal batch size for maximum OEE -
Capacity Planning:
Forecast of required capacity based on historical OEE values
Simulation of peak loads and their impact on OEE
Best Practices: Data Capture and Analysis for OEE Calculation
Structured data capture and analysis are essential for meaningful OEE calculations, ensuring accurate insights into manufacturing efficiency.
Structured Data Capture Plan for OEE
An effective data capture plan includes the following components:
-
Master Data:
- Definitions of all time categories (planned production, breaks, maintenance)
- Ideal cycle times per product
- Quality standards and tolerance limits
-
Transactional Data:
- Downtime with categorization
- Production quantities (input/output)
- Scrap and rework with error classification
-
Capture Intervals:
- Downtimes: Immediately upon occurrence
- Production quantities: Hourly or per shift
- Quality data: During quality checks or continuously
Data Aggregation and Analysis
For meaningful OEE analysis, data must be aggregated effectively:
-
Time-Based Aggregation:
- Shift-based for operational management
- Daily for tactical decisions
- Weekly for trend analysis
- Monthly for strategic management
-
Product and Equipment-Based Analysis:
OEE by Product Family:
- Product A: 82%
- Product B: 68%
- Product C: 75%
OEE by Shift Team:
- Team 1: 76%
- Team 2: 74%
- Team 3: 69% -
Drill-Down Capability: The ability to navigate from aggregated data to detailed levels is crucial for root cause analysis:
Total OEE Value → Factor with Greatest Loss → Main Loss Source → Specific Incidents → Detailed Analysis
Visualization of OEE Data
Effective visualization is critical for interpreting and communicating OEE data:
-
Operational Dashboards:
- Real-time display of current OEE and its components
- Time trend of the last hours/shifts
- Visualization of current downtimes and losses
-
Tactical Analysis Tools:
- Pareto charts of loss sources
- Trend analyses over multiple days/weeks
- Comparative analyses between products/shifts
-
Strategic Reports:
- Long-term trends in OEE development
- Correlation analyses with business KPIs
- ROI calculations for optimization measures
OEE Calculation Tools and Software Solutions
Various tools are available for practical OEE implementation, ranging from simple spreadsheets to advanced Manufacturing Execution Systems (MES).
Excel-Based OEE Calculation
For beginners and small businesses, Excel provides a good starting point:
Advantages:
- Low entry barrier
- Flexible customization to specific needs
- No additional software required
Disadvantages:
- Manual data entry
- Limited real-time capability
- Error-prone for complex calculations
Example Template Structure:
- Input sheet for production data
- Calculation sheet with OEE formulas
- Dashboard with visualizations
- Historical archive for trend analyses
Specialized OEE Software
Dedicated OEE software offers comprehensive features for professional applications:
Core Functions:
- Automatic data capture from machines
- Real-time OEE visualization
- Comprehensive analysis tools and reports
- Integration with existing systems
Selection Criteria:
- Scalability (number of capturable assets)
- Integration options (interfaces to machines and ERP)
- Mobility (access from tablets/smartphones)
- Customizability (calculation methods, dashboards)
MES-Integrated OEE Calculation
Manufacturing Execution Systems integrate OEE as part of holistic production control:
Advantages of Integration:
- Consistent data foundation for all production KPIs
- Bidirectional communication with ERP and planning systems
- Holistic process optimization beyond isolated KPI improvements
- End-to-end traceability of products and processes
Integration with Other KPIs:
- OEE values feed into KPIs like Overall Asset Effectiveness (OAE)
- Linkage with energy efficiency KPIs for sustainable optimization
- Correlation analyses with cost KPIs for economic evaluation
Cloud-Native OEE Solutions
Modern OEE solutions leverage cloud technologies for maximum flexibility and scalability:
Technical Advantages:
- Rapid implementation without complex IT infrastructure
- Automatic updates and extensions without system interruptions
- Cross-site access and benchmarking
- Flexible scaling with business growth
Functional Highlights:
- Multi-device access (PC, tablet, smartphone, shop floor displays)
- Modular expandability (OEE → Predictive Maintenance → APM)
- AI-based analytics with growing data volumes
- Open APIs for integration with existing systems
Conclusion: OEE Calculation as a Continuous Improvement Process
Calculating Overall Equipment Effectiveness is far more than a mathematical exercise—it is the cornerstone of sustainable productivity improvements in manufacturing.
The OEE Optimization Cycle
For long-term success, OEE calculation must be embedded in a continuous improvement process:
- Measure: Capture OEE data accurately and consistently.
- Analyze: Identify the largest loss sources using Pareto analysis.
- Improve: Implement targeted measures to reduce primary losses.
- Standardize: Establish new best practices as standards.
- Repeat: Restart the cycle with higher targets.
Critical Success Factors for OEE Calculation
Practical experience from numerous OEE implementations highlights these critical factors:
- Data Reliability: The accuracy of OEE values depends directly on the quality of data capture.
- Methodological Consistency: Standardize definitions and calculation methods company-wide.
- Leadership Support: OEE optimization requires commitment at all levels, especially from management.
- Employee Engagement: Train operators and maintenance staff on the significance and application of OEE.
- Technological Support: Leverage modern technologies for precise data capture and analysis.
From Measurement to Improvement: Implementing OEE in Practice
Identify Quick Wins
Start your OEE implementation by pinpointing high-impact areas for rapid improvements in manufacturing efficiency.
Develop a Data Strategy
Establish a robust data capture plan to ensure accurate OEE calculations and drive OEE optimization.
Foster Continuous Improvement
Embed OEE in a cyclical process to sustain continuous improvement and achieve lasting manufacturing transformation.
Ready to transform your production with OEE? Our platform empowers you to:
- Monitor OEE in real time
- Identify losses instantly
- Drive data-backed improvements