The Six Most Common OEE Mistakes and How to Avoid Them
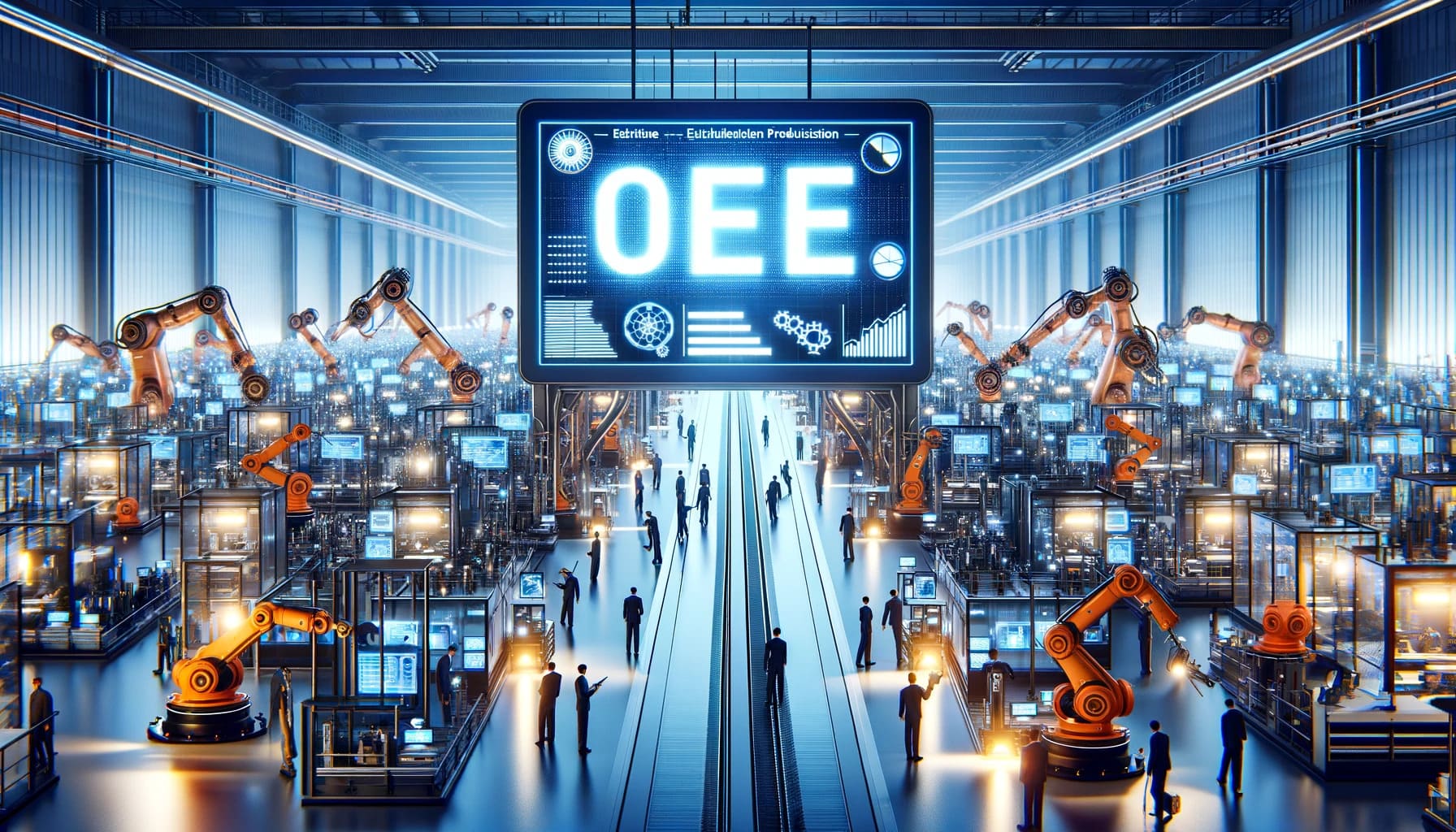
In the manufacturing industry, intensifying global competition has made effectiveness and efficiency more important than ever before. Whether or not a machine is optimally utilized can have a decisive impact on a company’s bottom line. In order to appropriately measure and evaluate overall efficiency, the instrument of “overall equipment effectiveness” is deployed. This metric is an essential part of production monitoring, because it allows straightforward determination of how production systems are performing while taking their availability, quality, and performance into account. To maximize the benefits of OEE, this instrument needs to be properly applied. Where are the biggest mistakes made in capturing data and using OEE? How can you eliminate them and leverage your OEE score to tangibly boost productivity?
Comparing the OEE scores of different processes
The fact that OEE is boiled down to a single figure often tempts managers to use it to compare different production systems or even different production facilities – without, however, taking their differing conditions and requirements into account. This inevitably leads to incorrect conclusions.
Comparisons of this kind really only make sense when evaluating equivalent machines that are used to make the same product in the same way. Comparisons should therefore always be made with caution. Make sure to meaningfully use OEE to measure how a machine’s productivity develops over a period of time and optimize the processes involved.
Calculating a OEE score for an entire production facility
There is also no point in figuring out the OEE score of an entire production site. Although this yields a value that summarizes the facility’s overall effectiveness, it doesn’t reveal any opportunities to make concrete improvements.
To have a realistic chance of identifying weaknesses and improving the situation, the metric should be broken down to a lower level. Start with a single machine and capture comparable metrics. From there, you can roll out the approach across your machines one at a time.
Choosing an excessively short time period
Production metrics are only truly informative when the examined time period is appropriately chosen. Excessively short periods, such as a single day or shift, often lead to incorrect results because it’s impossible to gather sufficient data in such a short time, and also because isolated events acquire too much weight.
It makes considerably more sense to calculate the metrics over a longer period of time. Over the course of a month, for example, productivity peaks and any downtimes can be smoothed into a much more useful result.
Excluding workers from the OEE implementation process
Workers play a central role in production; they operate the machines day after day and have a highly developed understanding of them. Consequently, after the causes of losses and opportunities for making improvements are identified with OEE, they should be the ones who take responsibility for implementing measures. If workers are excluded from the OEE implementation process, this can reduce their commitment and motivation. Open communication among all participants and appropriate data collection positively influence the improvement process. Because of this, it’s advisable to involve the entire production team, including machine operators, in the OEE implementation process. By bringing together expertise on different work areas, productivity gains can be achieved faster and more easily.
Focusing on the OEE score itself
The OEE metric is incredibly powerful. However, although it clearly reflects “what” happens in a machine, it doesn’t reveal “why” it happens. Unfortunately, many managers tend to focus too much attention on the OEE score without looking behind the scenes and identifying the causes of existing weaknesses with regard to availability, quality, and performance. They should change their perspective and leverage the OEE score as a call to action, because merely capturing it won’t in itself boost productivity. Decision-makers should derive measures for making improvements from this that eliminate the causes of production losses; the OEE score then improves automatically.
Capturing data by hand
One of the biggest mistakes made in connection with determining the OEE metric is collecting data by hand. Since production is becoming increasingly complex as a result of automation, digitalization, and globalization, manually collecting and calculating data is no longer appropriate.
Although it’s basically possible to work out a OEE score with paper and pencil or in an Excel spreadsheet, this approach is associated with certain risks and drawbacks. It starts with having machine operators manually record production values and downtimes. Inaccuracies can arise here because they’re trained to make sure that the machine runs without a hitch – but not for bookkeeping.
Without appropriate software, capturing, evaluating, and processing data is not only time-consuming but also error-prone. Completely automated monitoring by a software-based solution is significantly more reliable, precise, and cost-effective.
Although it’s basically possible to work out a OEE score with paper and pencil or in an Excel spreadsheet, this approach is associated with certain risks and drawbacks. It starts with having machine operators manually record production values and downtimes. Inaccuracies can arise here because they’re trained to make sure that the machine runs without a hitch – but not for bookkeeping.
Without appropriate software, capturing, evaluating, and processing data is not only time-consuming but also error-prone. Completely automated monitoring by a software-based solution is significantly more reliable, precise, and cost-effective.
Conclusions
As production processes become more complex, the challenge of monitoring, capturing, and analyzing OEE metrics is growing. This has to do with the quantity and complexity of the data involved, and also with the challenge of properly using them to derive measures for optimizing production processes.
OEE - Further information
Discover our selected articles on OEE and how it can revolutionize your production processes below:- Calculating OEE - Discover how you should go about calculating Overall Equipment Effectiveness and master the first steps to optimization.
- Six Big Losses - The most important causes of OEE losses - A detailed explanation of the 'Six Big Losses' that can occur in production and their impact on the OEE factors.
- The Benefits of automated OEE measurement - Automated OEE measurement assures you of high accuracy, consistent data, reliable real-time monitoring and much more.
- Why improving OEE lowers your production costs - Eliminating your sources of loss leads to cost savings and higher profits in addition to a higher OEE value.
- How to improve the OEE in your production - Learn how to increase the OEE value with your production team using an exemplary improvement process.
- Why OEE is one of the most important production metrics! - If your goal is to achieve more profitable production, then you should definitely know to what extent the OEE key figure can help you achieve this.
- What characterizes a good OEE score? - The determined OEE value can be a warning signal, an indication of average levels or an award.
OEE is a decisive factor for Lean Production, Continuous Improvement (CIP), Kaizen, Six Sigma and Shopfloor Management. It plays a central role in the identification and utilization of improvement potentials in production. OEE solutions enable efficient communication and coordination at the production level, which is essential for the rapid identification and elimination of problems.
Get started with OEE today
SYMESTIC is one of the world's leading providers of OEE-based system solutions. Take the opportunity for a no-obligation 4-week evaluation and see for yourself the simplicity, efficiency and cost savings that our OEE Software-as-a-Service offers. Experience how OEE and other important key figures can be automatically recorded, calculated and analyzed. Benefit from objective, trustworthy metrics, dashboards, reports and notifications that support all departments of your company close to production.
Discover the power of the most advanced manufacturing software and make your production more efficient tomorrow!