Lean Production Guide: Principles, Methods, and Industry 4.0 Integration
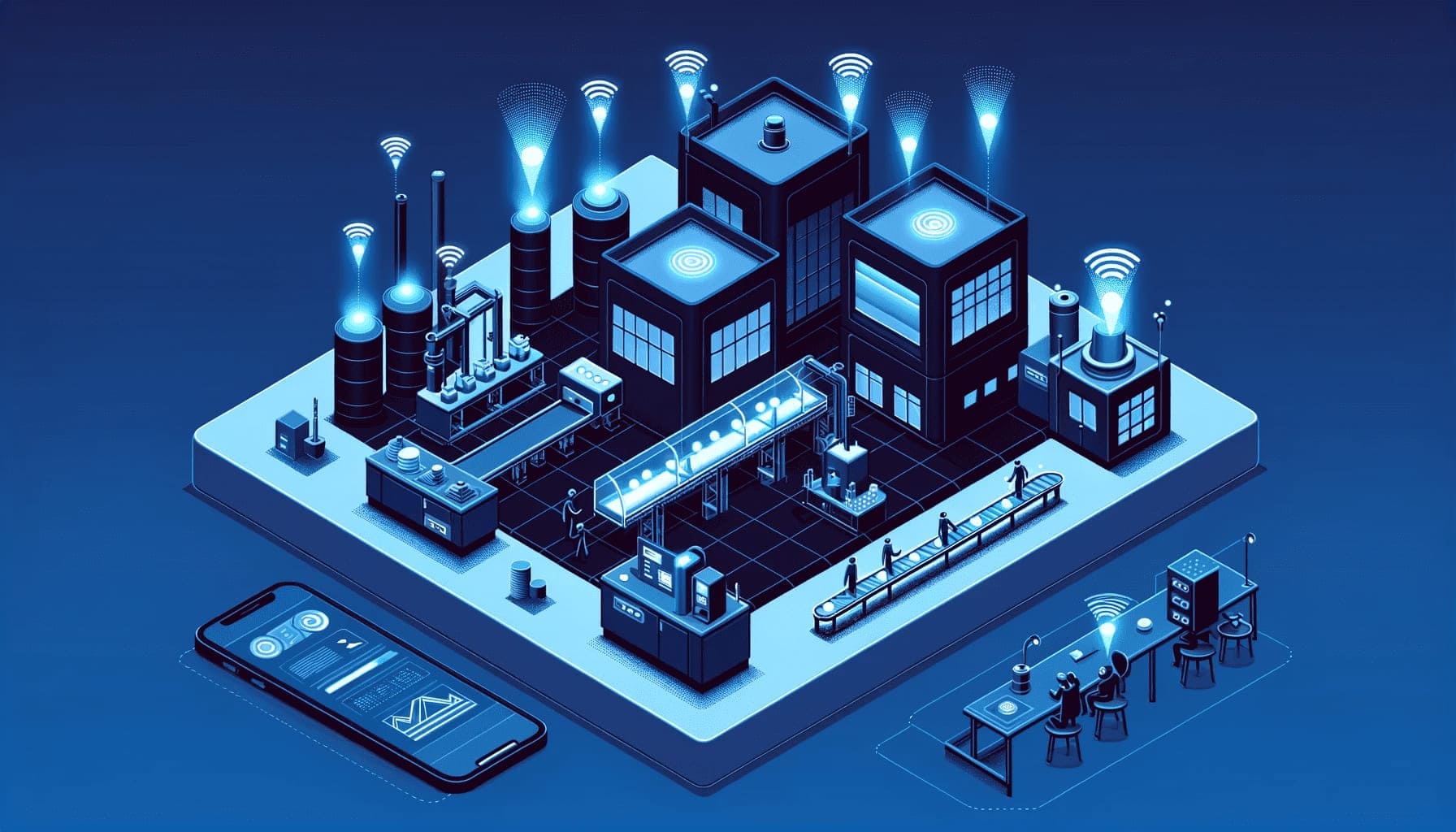
Lean Production Guide: Principles, Methods, and Industry 4.0 Integration
In this comprehensive guide, discover how your company can benefit from Lean Production. From core principles to implementation steps and Industry 4.0 integration – find all the essential information for successful execution. Learn how to eliminate waste, optimize processes, and achieve up to a 25% productivity increase.
Transform Your Production with Symestic
Elevate your Lean Production with Symestic Cloud MES – achieve up to 70% reduced lead times, 60% lower quality costs, and real-time process optimization. Start your 30-day free trial today!
Start Your Free Trial Now!What is Lean Production?
Lean Production (also known as Lean Manufacturing) is a holistic management approach aimed at systematically eliminating waste and continuously optimizing production processes. Originating in the 1950s at Toyota, it is now a cornerstone for increasing competitiveness, particularly in the context of Industry 4.0.
The 3 Core Principles of Lean Production
Maximum Value Creation
All activities are consistently aligned with customer benefit.
Minimum Waste
Systematic elimination of non-value-adding activities.
Continuous Improvement
Constant optimization of all processes through the Kaizen principle.
Significance for US Companies
In times of global competition, increasing customer demands, and digital transformation, Lean Production is more important than ever for US companies. Studies show that companies implementing Lean methods can achieve:
- 15-25% increase in productivity
- 50-70% reduction in lead times
- Up to 60% reduction in quality costs
- 30-50% optimization of inventory levels
The 5 Core Principles of Lean Production
Define Value
Determine customer benefit and focus on value-creating activities. Only processes that create value from the customer's perspective should be maintained.
Identify Value Stream
Analyze all process steps to distinguish between value-adding and non-value-adding activities. Eliminate waste like unnecessary waiting times or duplicate workflows.
Establish Flow
Create a continuous material flow to avoid waiting times and optimize lead times through smooth coordination of production steps.
Implement Pull Principle
Produce only when there is concrete demand, controlled by actual customer orders, to prevent overproduction and reduce inventory costs.
Strive for Perfection
Continuously improve all processes through Kaizen, involving the entire workforce in regular optimizations.
Practice Tip: Establish regular Kaizen workshops to develop and implement improvement measures.
The 8 Types of Waste in Lean Production
In Lean Production, there are eight main types of waste (Japanese: "Muda") that need to be eliminated to optimize processes and reduce costs.
Overproduction
Production beyond demand, causing unnecessary capital tie-up and storage costs. It leads to further inefficiencies.
Inventory
Excessive inventory ties up capital and masks process problems, increasing storage costs and risks of obsolescence.
Waiting Times
Unsynchronized processes lead to waiting times that increase throughput time due to poor planning or missing resources.
Transport
Unnecessary transport routes waste time and increase the risk of damage due to suboptimal factory layouts.
Over-processing
Processing beyond customer requirements wastes resources, often due to unclear specifications.
Motion
Unnecessary employee movements are inefficient and pose ergonomic strain. Use ergonomic workplace design to mitigate.
Practice Tip: Organize workplaces using the 5S methodology to reduce unnecessary movement.
Defects
Quality defects cause rework, warranty cases, and complaints, leading to both direct and indirect costs.
Unused Potential
Employee knowledge and creativity are underutilized. Involve employees in continuous improvement processes.
Best Practice: Companies with active idea management generate 10-12 improvement suggestions per employee per year.
Key Lean Methods in Practice
Successful implementation of Lean Production relies on proven methods and tools that form a comprehensive system for production optimization.
Just-in-Time (JIT)
Produce based on demand to minimize inventory and increase flexibility. Learn more about JIT.
Kanban
Visualize material flow and control production to prevent overproduction. Explore Kanban.
Digitalization Insight: Modern e-Kanban systems enable digital control of material flows.
5S Methodology
A systematic approach to workplace organization. Learn the five steps.
Practice Tip: Visualize 5S standards through photos and checklists.
Value Stream Mapping
Visualize the production process to identify and eliminate waste, documenting current and future states.
SMED
Reduce setup times with SMED to enable smaller batch sizes and increase flexibility.
Total Productive Maintenance (TPM)
Optimize equipment effectiveness with TPM to minimize downtime.
Benefits of Lean Production
Successful implementation of Lean Production leads to measurable improvements in various areas, enhancing overall efficiency and competitiveness.
Quality Improvement
Reduce error rates and improve product quality. Error rates can drop by up to 90%.
Efficiency Gains
Boost productivity by 15-25% and reduce lead times by up to 70% through streamlined processes.
Cost Savings
Lower production and quality costs while optimizing inventory costs with better resource utilization.
Implementation of Lean Production
The introduction of Lean Production requires a systematic approach in several phases to ensure sustainable success.
Preparation
Secure top management commitment and provide comprehensive training to employees to embrace the Lean philosophy.
Pilot Project
Start with a current state analysis and test Lean methods in selected areas to gain experience.
Best Practice: Choose an area with high optimization potential and motivated employees for your pilot.
Standardization and Rollout
Standardize successful approaches and gradually extend to other areas with clear work instructions.
Sustainable Integration
Lean Production is a permanent change in corporate culture. Use Shopfloor Management to anchor Lean thinking.
Lean Production & Industry 4.0
The integration of Lean Production with Industry 4.0 offers new opportunities for production optimization. Modern technologies enhance Lean principles and streamline processes.
- Digital Shopfloor Boards: Enable real-time visualization and cross-site transparency for better coordination.
- Digitalization Tip: Start digitalization where it brings the greatest benefit to your Lean activities, such as KPI tracking.
- Smart Kanban: Use RFID technology for automatic reordering and efficient material replenishment.
- Connected Machines: Support Predictive Maintenance to reduce downtime and increase machine availability.
Combining Lean Production with Industry 4.0 creates a foundation for future-proof, efficient production. Keep it as simple as possible to avoid unnecessary complexity.
Summary: Lean Production eliminates waste, optimizes processes, and integrates seamlessly with Industry 4.0 technologies, driving significant efficiency and cost savings.