What Is Operational Excellence? - Definition, Strategy & Approach
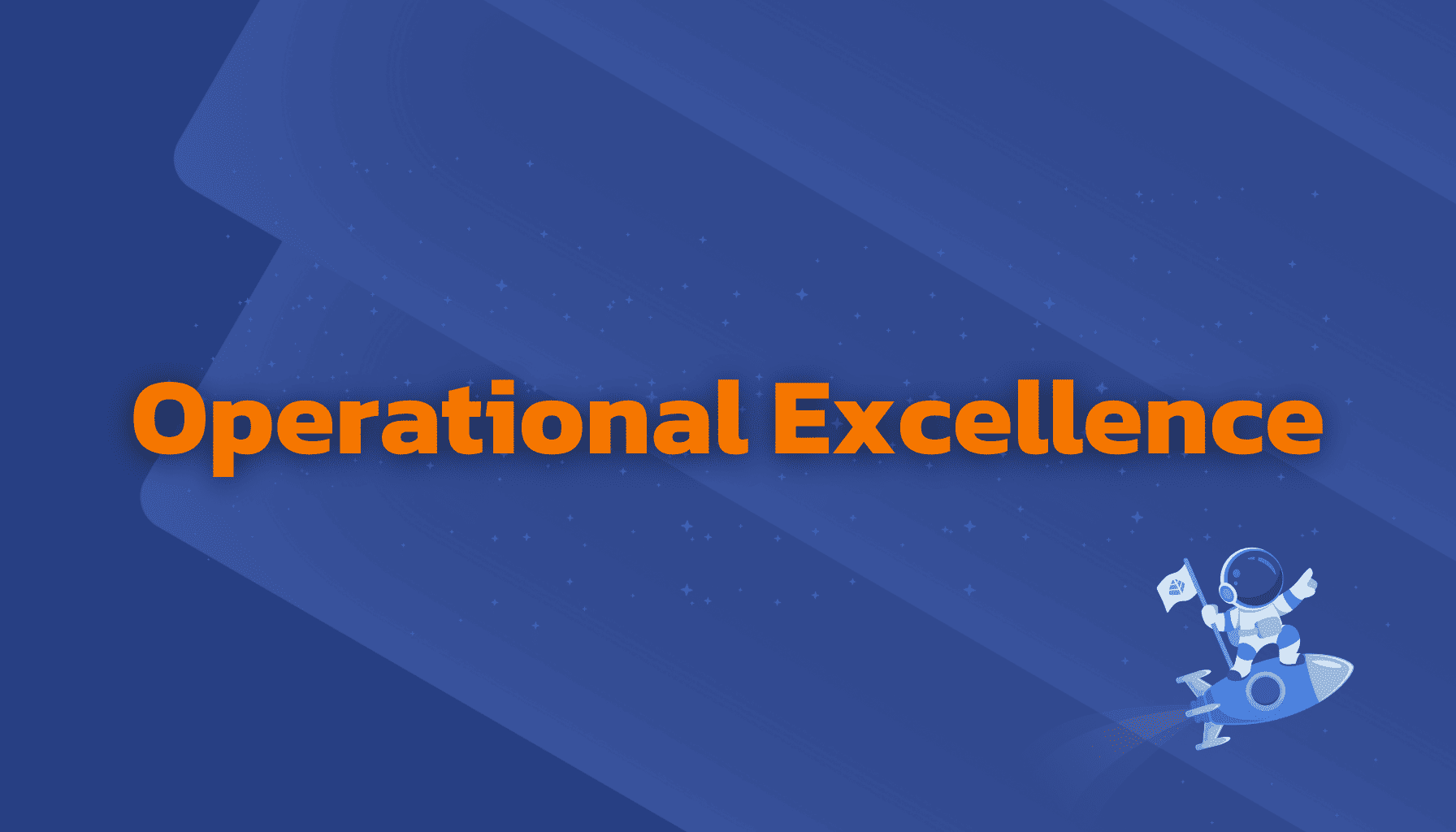
- Operational excellence: definition
- Evolutionary process of operational excellence
- Operational excellence in the age of digitalization
- Successful operational excellence application examples
- Benefits and risks of operational excellence
- Strategy, approach and phases for the introduction of operational excellence
- Measuring and Achieving Operational Excellence
- Operational excellence toolbox
What is Operational Excellence?
Operational excellence is a multidimensional management concept that aims to achieve continuous improvement in all areas of a company. At the core of operational excellence lies the principle of lean management philosophy, which aims to minimize waste and maximize value for the customer.
This is achieved through the application of Six Sigma methods, which are designed to reduce errors and improve quality. This holistic management approach integrates proven methods such as Total Quality Management to ensure perfect alignment of company activities with strategic goals.
Operational excellence includes process standardization, continuous improvement, performance measurement and a strong focus on customer satisfaction. It also promotes a culture of continuous improvement and innovation. This enables companies to adapt to changing market conditions and integrate new technologies. It is not a one-off project, but an ongoing, company-wide initiative aimed at sustainably increasing competitiveness and long-term business success.
The management approach of Operational Excellence is crucial for success in a constantly changing business world.
Cloud MES: Revolutionize Your Production
In a world that demands speed, efficiency, and innovation, Cloud MES is your key to digital manufacturing. Discover how you can redefine your processes, reduce costs, and outperform the competition with cloud-native solutions like SYMESTIC.
Global Scalability
Effortlessly adapt your manufacturing to new markets.
Quick Results
Implement in weeks, not months.
Intelligent Processes
Leverage AI for precise analysis and optimization.
Try SYMESTIC free for 30 days and experience the future of manufacturing!
Evolutionary process of operational excellence
The emergence and development of Operational Excellence (OpEx) can be described as an evolution of various management theories and practices over several decades. This development was significantly influenced by the drive for efficiency, quality and customer orientation in the business world.
Early influences (early 20th century):
The foundations for operational excellence were laid at the beginning of the 20th century. Frederick W. Taylor's principles of scientific management, also known as "Taylorism", were pioneering. Taylor focused on increasing efficiency through the standardization of work processes and time studies.
Lean manufacturing and Toyota Production System (mid-20th century):
Another milestone was the development of lean manufacturing and the Toyota Production System (TPS) in Japan after the Second World War. These approaches aimed to eliminate waste, optimize processes and improve quality. They laid the foundation for many principles that are now summarized under operational excellence.
Total Quality Management (TQM) (1950s to 1980s):
Total Quality Management (TQM) became increasingly important between the 1950s and 1980s. TQM focused on comprehensive quality improvement in all areas of the company and integrated customer satisfaction as a central aspect. The work of quality experts such as W. Edwards Deming and Joseph Juran played an important role in this.
Start Your Free Trial Today
Discover how SYMESTIC’s cloud-native platform transforms your production. Try it free for 30 days – no commitment, instant setup.
Try Free for 30 DaysSix igma (1980s):
In the 1980s, Motorola introduced Six Sigma, a data-driven approach to minimizing defects and improving quality. This approach was quickly adopted by other leading companies such as General Electric.
Integration and expansion (1990s to present):
Throughout the 1990s and beyond, companies began to integrate elements from lean manufacturing, TQM, Six Sigma and other management approaches to create holistic systems for improving operational excellence. This led to the development of comprehensive operational excellence programs that emphasize not only efficiency and quality, but also flexibility, innovation and continuous improvement.
Digitalization and Industry 4.0 (21st century):
In the 21st century, digitalization and the development of Industry 4.0 has led to new opportunities and challenges for operational excellence. The use of big data, artificial intelligence and automated processes opens up new ways to optimize processes and increase efficiency.
Operational excellence in the age of digitalization
Digital transformation has not only changed the way companies operate, but has also redefined the foundations of operational excellence. In this section, we will dive deeper into the impact of digitalization on operational excellence, specifically addressing the challenges and opportunities that arise in this rapid technological change.
-
The key role of digitalization in operational excellence
The integration of data analysis, artificial intelligence (AI) and automation is not only a way to increase the efficiency of business processes, but also marks a paradigm shift in the implementation of operational excellence. Data-driven decision-making processes enable more precise process optimization, while AI-supported systems can react to changes in real time. Companies that use these technologies skillfully can not only increase their operational efficiency, but also react more flexibly to changing market conditions.
-
Communication tools and operational excellence
In the course of digitalization, effective communication is becoming increasingly important. Initially, emails were widely used as a means of communication for transmitting information and as a tool for promoting operational excellence initiatives. Modern cloud-based manufacturing platforms are replacing traditional email communication with their specific communication and information features. By sharing best practices, challenges and solutions, companies can create a learning organization that continuously benefits from internal and external insights.
-
Operational excellence in an international context
Globalization presents companies with the challenge of applying operational excellence methods to international business processes. Successful implementation requires targeted adaptation to cultural differences and regulatory requirements in different countries. As a pioneer in Industry 4.0, Germany is increasingly focusing on the development of global operational excellence strategies and the formation of international networks in order to master the challenges of global markets.
-
Partnerships and networks: Strong together in Operational Excellence
Collaboration with partners and the formation of networks are no longer just supporting elements, but crucial components of a successful operational excellence strategy. Through joint projects and the exchange of best practices, companies can go beyond their own borders and create synergies. Especially in the context of Industry 4.0 projects, partnerships play a crucial role in driving innovation and optimizing the entire value chain.
Start Your Free Trial Today
Discover how SYMESTIC’s cloud-native platform transforms your production. Try it free for 30 days – no commitment, instant setup.
Try Free for 30 DaysSuccessful operational excellence application examples
General Electric (GE), a global leader in industrial manufacturing and technology, has successfully implemented Operational Excellence as an integral part of its business strategy. Here are some specific actions GE has taken:
1. process optimization in manufacturing:
GE has implemented extensive process optimization to increase the quality of its products while reducing production costs. This has included the introduction of lean methods that have helped to minimize waste and create more efficient manufacturing processes.
2. continuous improvement:
The company has fostered a culture of continuous improvement by integrating Kaizen principles into its way of working. Employees at all levels have been encouraged to constantly look for ways to increase efficiency and improve quality.
3. efficient supply chain:
GE optimized its supply chain to reduce delivery times and increase reliability. This has enabled the company to better meet customer needs and strengthen its market position.
4. customer centricity:
A strong emphasis on customer satisfaction was a cornerstone of operational excellence at GE. This led to the development of products and services that focused on customer needs.
The implementation of Operational Excellence at General Electric not only served to optimize internal processes, but also to develop innovative solutions and services. This helped GE to differentiate itself from its international competitors and increase its global competitiveness. This example shows how deeply operational excellence can be implemented in a company to achieve concrete results in terms of efficiency, quality and competitiveness.
Benefits and risks of operational excellence
Benefits of Operational Excellence
- Increased efficiency: By optimizing and standardizing processes, efficiency is increased, resulting in faster execution and lower operating costs.
- Quality improvement: Applying principles such as Six Sigma leads to higher quality products and services, which in turn increases customer satisfaction.
- Cost reduction: By minimizing waste, errors and inefficiencies, companies can significantly reduce their costs.
- Increasing customer satisfaction: A strong focus on customer needs and expectations helps to increase customer satisfaction and loyalty.
- Flexibility and adaptability: Companies that pursue operational excellence are better able to adapt quickly to market changes and new challenges.
- Employee engagement and satisfaction: Involving employees in improvement processes and promoting a culture of continuous improvement increases employee engagement and satisfaction.
- Risk minimization: Efficient and standardized processes reduce the risk of errors and failures, which in turn increases the reliability of operations.
- Sustainability: Operational excellence can also lead to more sustainable operating practices by using resources more efficiently and reducing waste.
- Improved competitiveness: The combination of cost reduction, quality improvement and customer satisfaction helps to strengthen the company's competitive position.
- Long-term value creation: Through continuous improvement and adaptation, companies create long-term value both for themselves and for their customers.
Risks of Operational Excellence:
- Resistance to change: Employees may resist changes introduced as part of operational excellence initiatives. This can lead to conflict, low morale and loss of productivity.
- Excessive standardization: Too much emphasis on standardization can limit creativity and innovation. There is a risk that companies become too rigid and inflexible to respond to changing market demands.
- Short-sightedness when it comes to cost savings: Too much focus on short-term cost savings can undermine long-term investment in growth and innovation.
- Overburdening employees: Operational excellence programs can lead to an excessive workload for employees, especially if they are implemented without adequate resources or support.
- Underestimating the resources required: Implementing operational excellence requires time, money and commitment. Underestimating these resources can lead to incomplete or unsuccessful implementations.
Strategy, approach and phases for the introduction of operational excellence
Implementing a management system for operational excellence in an organization is a complex process that requires careful planning, execution and monitoring. Here are the basic strategies, procedures and phases that are typically followed when introducing such a system:Strategy
- Clearly define the objectives: Define what operational excellence means to your organization and what specific goals are to be achieved (e.g. cost reduction, quality improvement, customer satisfaction).
- Top management commitment: Ensure that the company management is fully behind the program and provides the necessary resources.
- Culture and mindset: Develop a culture of continuous improvement that is shared by all employees.
- Integration into business strategy: Ensure that operational excellence is integrated into the company's overall business strategy.
Approach
- Needs analysis and current state assessment: Determine the current state of processes and identify areas for improvement.
- Employee involvement: Create awareness of the importance of operational excellence and involve employees at all levels in the process.
- Selection of methods and tools: Select suitable methods and tools (e.g. Lean, Six Sigma) that match the objectives and corporate culture.
- Training and skills development: Invest in training and development for your employees to develop the necessary skills.
Phases of implementation
Planning phase:
- Establish the goals and scope of the program.
- Form a core team to manage the program.
- Develop a detailed implementation plan.
Implementation phase:
- Start with pilot projects to test the concepts and achieve rapid success.
- Gradual expansion to other areas of the company.
- Continuous monitoring and adjustment of strategies and processes.
Consolidation phase:
- Anchoring the new processes and practices in day-to-day business.
- Strengthening the culture of continuous improvement.
- Regular review and adaptation of processes.
Maturity phase:
- Operational excellence becomes an integral part of the corporate culture.
- Continuous improvement and innovation are established practices.
- Regular benchmarking and adaptation to new challenges and technologies.
The successful introduction of operational excellence requires time, patience and ongoing commitment. It is an iterative process that aims to bring about long-term change and sustainably improve the company's competitiveness.
Measuring and Achieving Operational Excellence
Operational excellence focuses on establishing quantifiable metrics to evaluate organizational performance. To measure operational excellence effectively, companies must implement a comprehensive framework of financial metrics and operational indicators:
Key Performance Areas:
- Employee productivity rates
- Process efficiency metrics
- Quality assurance indicators
- Customer satisfaction scores
- Financial performance measures
Companies should establish baseline measurements across these dimensions to track sustainable improvement over time. This enables organizations to make informed decisions based on concrete data rather than assumptions.
Core Principles and Cultural Foundation
The principles of operational excellence are deeply integrated into organizational culture and daily business operations. These core principles include:
- Customer-Centric Operations
- Alignment with customer demand
- Value stream optimization
- Service level excellence
- Process Excellence
- Systematic process mapping
- Continuous workflow optimization
- Quality assurance protocols
- Employee Engagement
- Performance management systems
- Skill development programs
- Recognition frameworks
- Strategic Alignment
- Clear business objectives
- Resource optimization
- Competitive advantage development
Building a Strong Company Culture
Achieving higher customer satisfaction and improved company productivity requires establishing a robust company culture focused on excellence:
Cultural Elements:
- Clear performance expectations
- Empowered decision-making
- Continuous learning environment
- Innovation mindset
- Quality-first approach
Implementation Framework:
- Leadership commitment
- Employee engagement programs
- Communication protocols
- Performance recognition systems
- Continuous improvement mechanisms
Operational Excellence Maturity Model
Organizations can assess their operational excellence journey through a structured maturity model:
Level 1: Foundation
- Basic process documentation
- Initial quality controls
- Standard operating procedures
Level 2: Development
- Process optimization initiatives
- Performance measurement systems
- Employee training programs
Level 3: Integration
- Cross-functional coordination
- Advanced analytics implementation
- Systematic problem-solving
Level 4: Optimization
- Predictive analytics
- Automated process controls
- Innovation integration
Level 5: Excellence
- Industry leadership
- Benchmark performance
- Sustainable competitive advantage
Performance Measurement Framework
To assure quality and improve efficiency, organizations must implement comprehensive measurement systems:
Key Metrics Categories:
- Operational Metrics
- Process cycle times
- Equipment effectiveness
- Resource utilization
- Quality Metrics
- Defect rates
- First-pass yield
- Customer complaints
- Financial Metrics
- Cost per unit
- Return on investment
- Operating margins
- Employee Metrics
- Productivity rates
- Satisfaction levels
- Training effectiveness
Advanced Implementation Strategies
To achieve sustainable improvement and maintain competitive advantage, organizations should focus on:
- Digital Transformation
- Advanced analytics implementation
- Real-time monitoring systems
- Automated workflow management
- Process Excellence
- Value stream optimization
- Waste elimination
- Quality management systems
- Workforce Development
- Skill enhancement programs
- Leadership development
- Performance management
- Innovation Management
- Continuous improvement programs
- Technology adoption
- Market adaptation strategies
Operational excellence toolbox
Operational excellence is much more than a methodology - it is a holistic and future-oriented approach to corporate management. It enables organizations to meet challenges efficiently and directly at the source in order to achieve significant improvements in both production and service processes. Operational excellence creates a robust foundation for operational excellence by managing and continuously improving processes at the point of value creation. Clear leadership, the active involvement of employees and the use of advanced metrics and technologies for visual management and process control are crucial to this.
In an era where efficiency, sustainability, timeliness and quality are key elements for business success, operational excellence offers companies a decisive advantage. It promotes a culture of continuous improvement and helps companies to strengthen their competitive position in the long term.
The integration of Total Productive Maintenance, Target Costing and Lean Management methods within the Operational Excellence toolbox enables companies to increase the efficiency and quality of their processes in a targeted manner.